Schnelle und präzise Technologien von langer Lebensdauer
Die Warmumformung, auch Presshärten, kommt zum Einsatz um besonders hochfeste Karosserieteile zu fertigen. Im Front of Line werden Platinen klassisch vereinzelt und anschließend durch einen Ofen gefördert, wobei sie Temperaturen von über 900° C annehmen. Anschließend werden sie hochtemperiert umgeformt. Hier kommt es auf schnelle Beladezeiten an, um ein zu starkes Abkühlen zu vermeiden. Die Anwendung ist daher ideal für die traversierenden Feeder-Systeme. Im vergangenen Jahrzehnt hat SIEMPELKAMP Transport Systems zahlreiche Warmumformanlagen in verschiedenen, standardisierten Ausbaustufen erfolgreich automatisiert. Dabei kommen je nach Anforderungen grundsätzlich zwei verschiedene Lösungen zum Einsatz – das Feeder- und das Transferkonzept.
Systemübersicht
Front of Line
Pressenbe- und Entladung
Front of Line: Aufbau
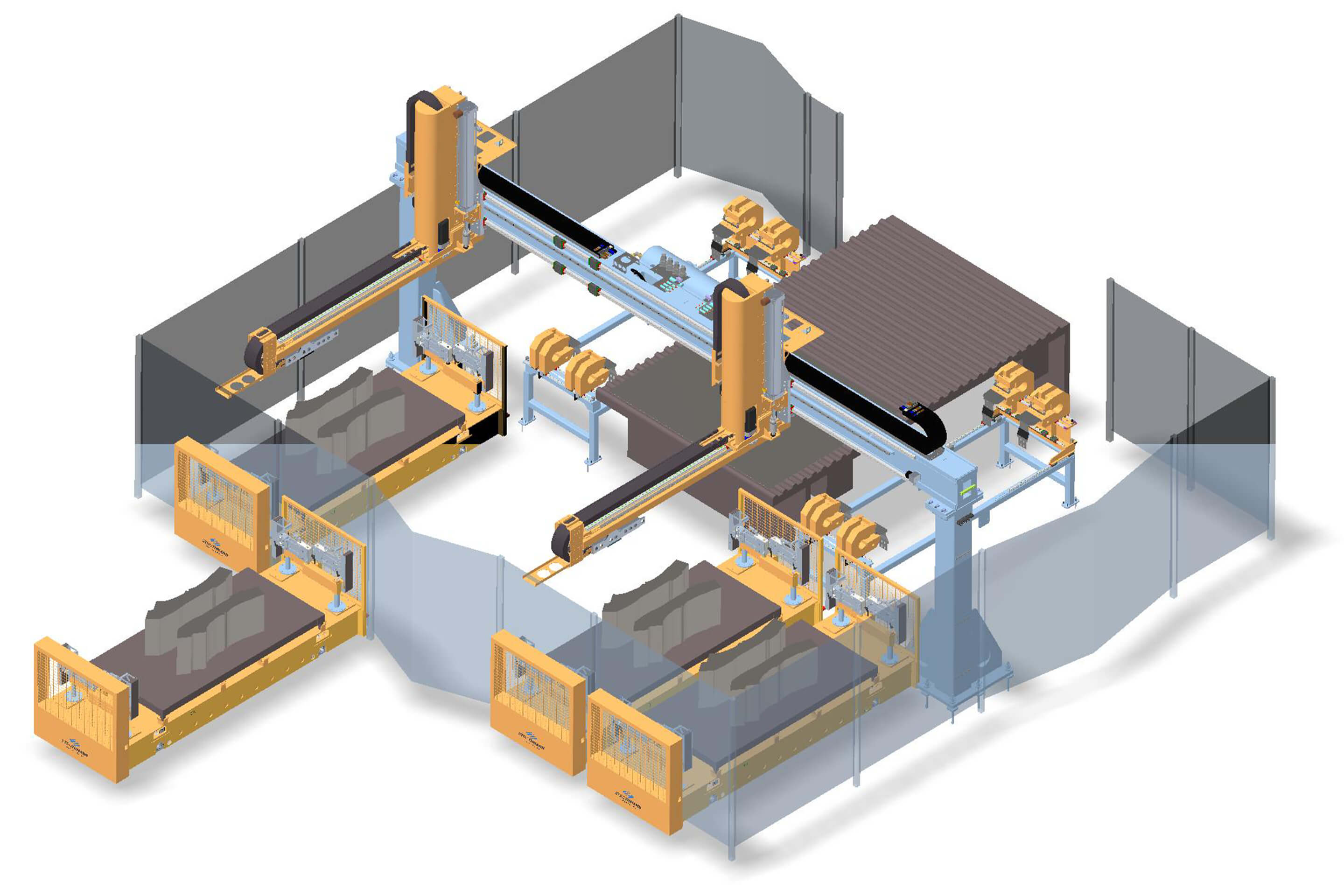
Platinenzufuhr auf vier angetriebenen Platinenwagen auf der RundSchiene (unterbrechungsfreier Stapelwechsel). Zaunelemente am Wagen schließen Schutzkreis
Spreizeinheiten auf Platinwagen manuell einstellbar
Entstapel-Feeder 3-080 mit zwei Feeder-Modulen und zusätzlicher C-Achse. Nutzlast 60 kg
Hydraulische oder pneumo-hydraulische Markierstation inklusive Doppelblechmessung. Zentriernest integrierbar
Ofenrollengang (Beistellung Kunde)
Technische Daten
Taktzeit |
Bis zu 10 s |
max. Nutzlast |
60 kg |
Platinenlänge |
2500 mm |
max. Stapelgewicht Palette |
6.000 kg |
Drehachse Destacker |
± 135° |
Anzahl Platinen pro Feeder |
2 |
Anzahl Markierungen Platine |
4 |
Presskraft Markieren |
120 kN |
Prozesszeit Markieren |
ca. 1,5 s |
Anzahl Letter |
bis zu 26 |
Pressenbe- und Entladung
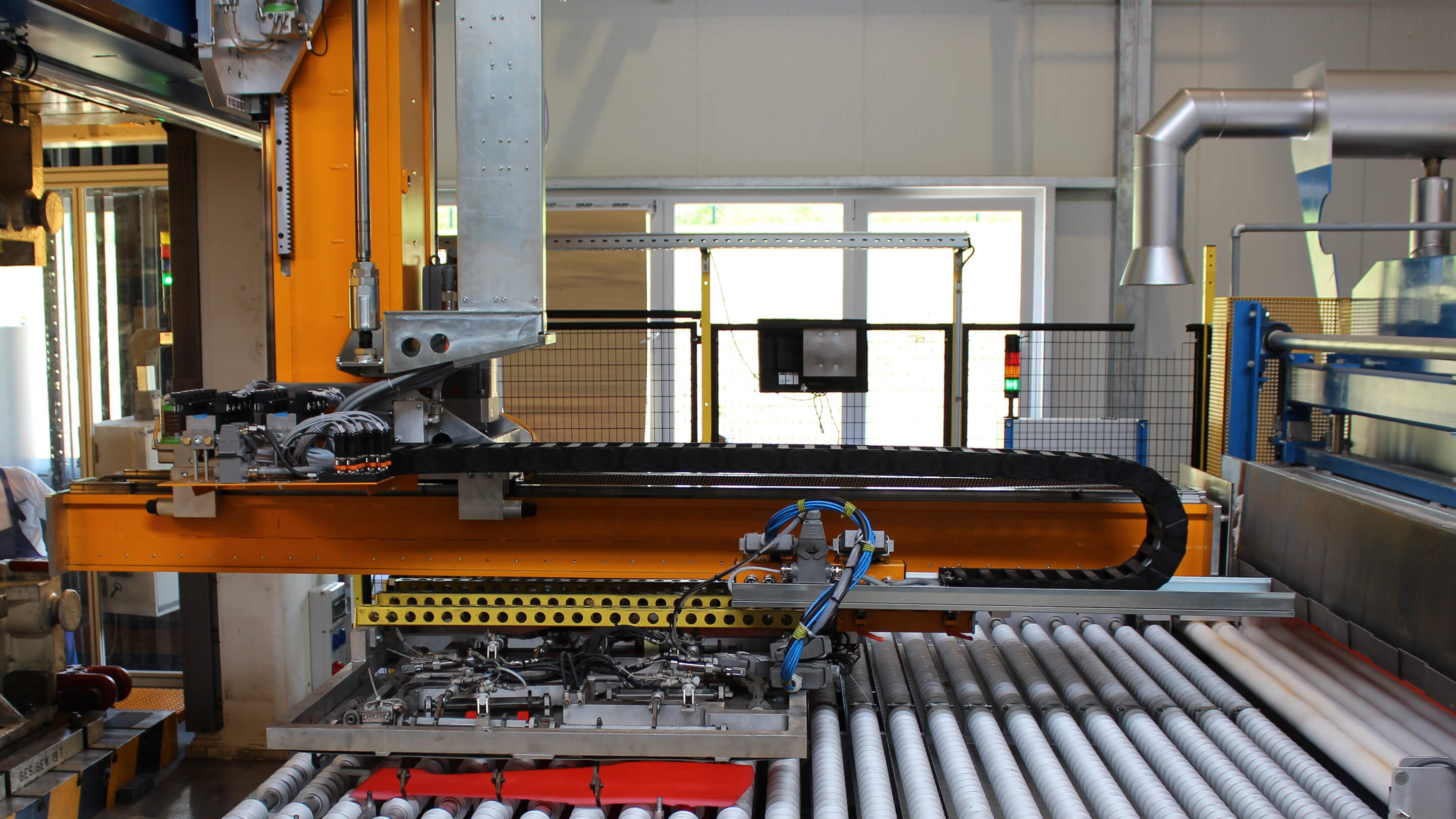
Feeder-Konzept
- Presse in Ofen-Durchlaufrichtung
- Be- und Entladung durch jeweils einen Feeder mit 200 kg bzw. 120 kg Traglast
- Großflächige Toolings mit Hitzeabschirmung
- Erreichbare Wechselzeit ca. 4 s
- Vorteil: kompakter Bauraum und geringere installierte Leistung
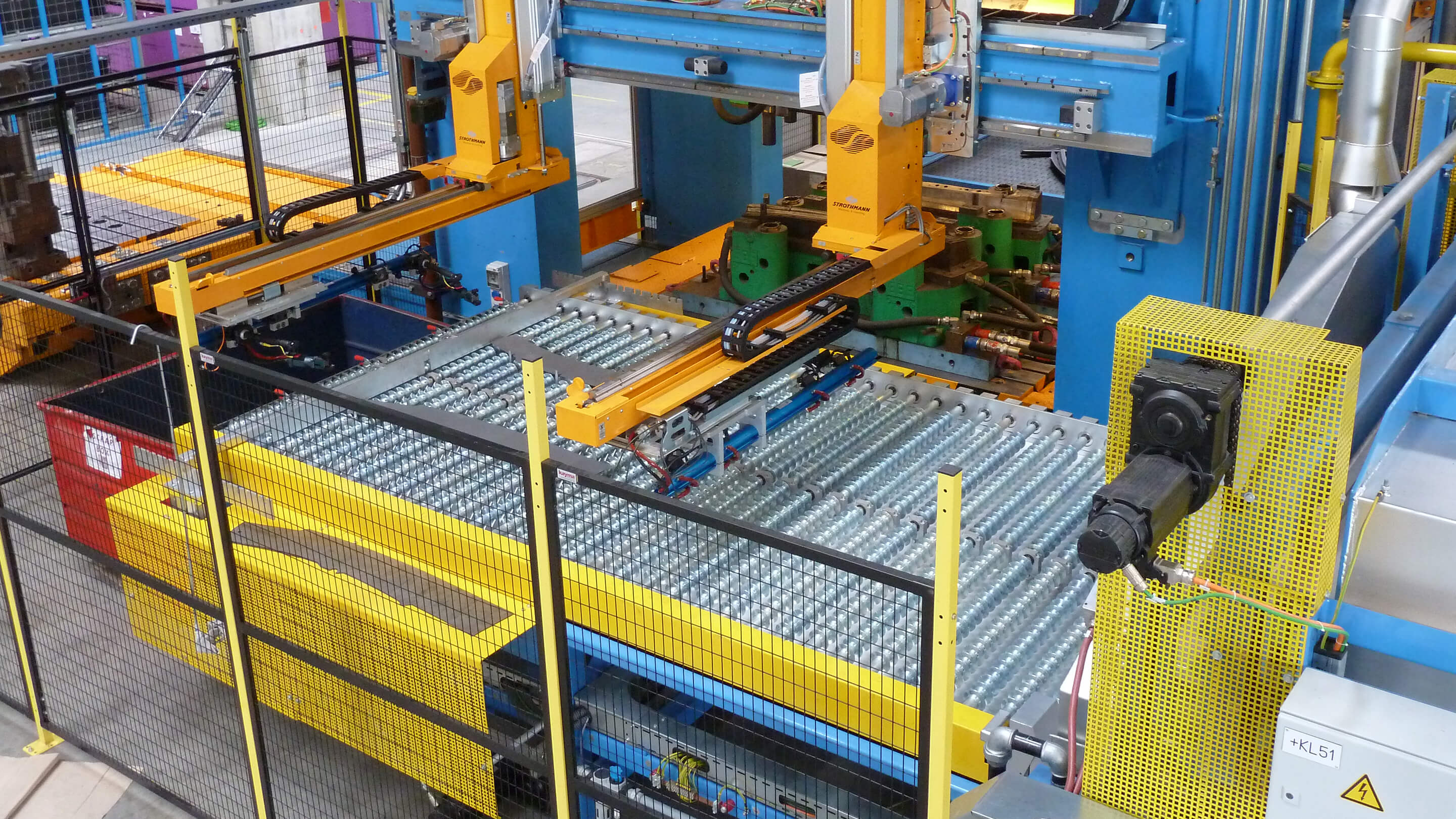
Transfer-Konzept
- Presse quer zur Ofen-Durchlaufrichtung
- Be- und Entladung durch jeweils zwei Feeder mit je 80 kg Traglast
- Feeder warten im Pressenraum neben den Werkzeugen
- Erreichbare Wechselzeit ca. 2,5 s
- Vorteil: minimale Taktzeiten
Feeder-Konzept |
Transfer-Konzept |
|||||
---|---|---|---|---|---|---|
Baugröße |
1 |
2 |
S |
M |
L |
XL |
Automationsgerät |
3/200 (Belader) |
3/200 |
3/040 |
3/040 |
3/080 |
3/080 |
max. Hub X |
3500 mm |
bis 6000 mm |
2500 mm |
3300 mm |
4000 mm |
4700 mm |
Standard-Hub Z |
1100 mm |
1100 mm |
700 mm |
700 mm |
800 mm |
800 mm |
Traglast |
200 kg |
120 kg |
2 x 40 kg |
2 x 40 kg |
2 x 80 kg |
2 x 80 kg |
erreichbare |
4 s |
4 … 4,5 s |
2,5 s |
2,5 s |
2,5 … 3 s |
3 s |