Hot forming: Quick, precise and long-lived technologies
Hot forming, including press hardening, is used to produce high-strength car body parts. In the Front of Line, blanks are separated in the conventional manner and then transported through a furnace where they are heated to a temperature of over 900°C. They are then formed while still hot. Quick loading times are crucial for this process to prevent excessive cooling. That makes traversing feeder systems ideal for this application. Throughout the past decade, SIEMPELKAMP Transport Systems has successfully automated numerous hot forming plants in a variety of standardized stages of expansion. Depending on the requirements SIEMPELKAMP uses two different basic solutions – the feeder and the transfer concept.
System overview
Front of Line
Press loading and unloading
Front of Line: Layout
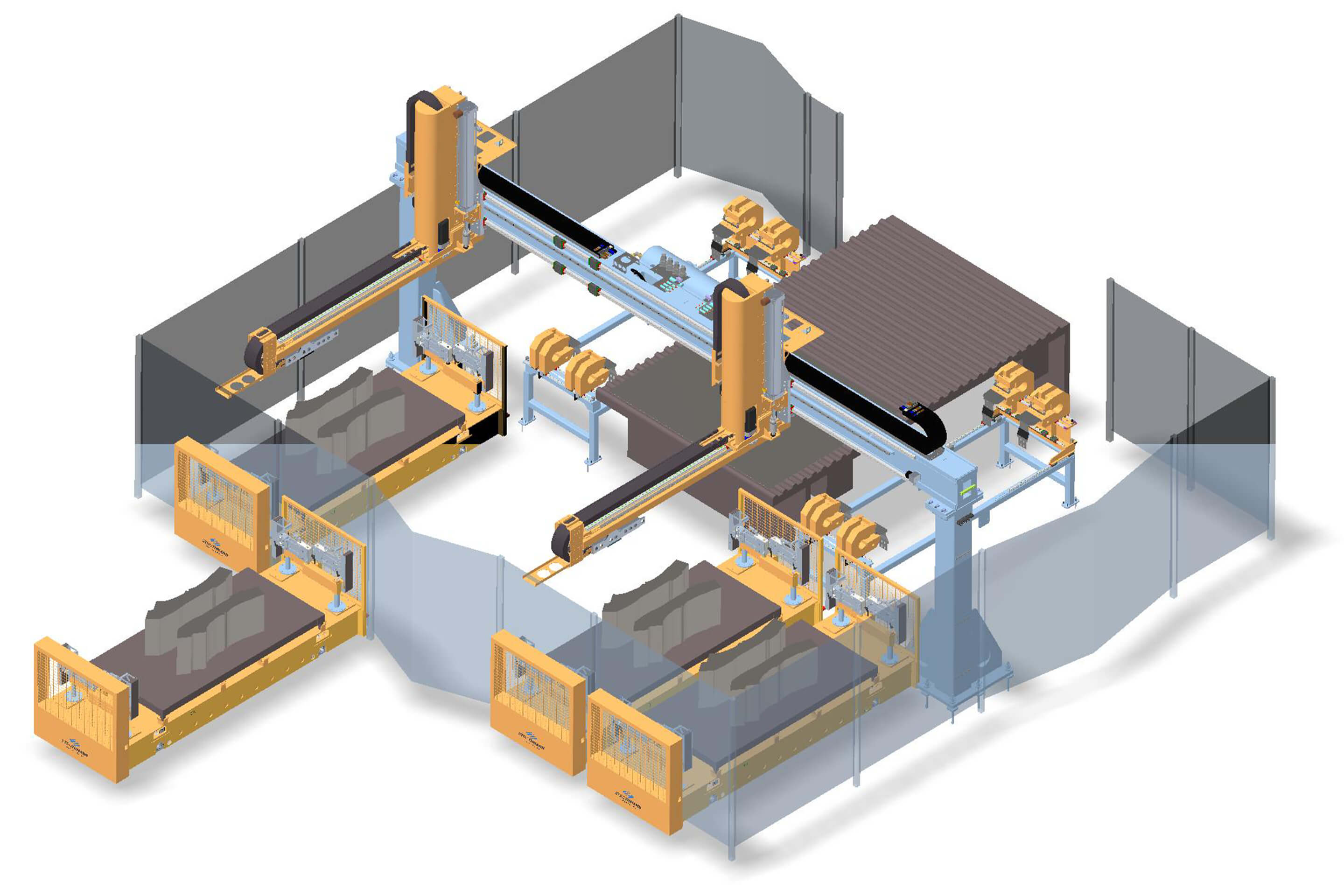
Blank feeding on four powered blanks carts on the RoundTrack (uninterrupted stack change). Fence elements on the cart close the protective circuit
Spreading units on blank carts are manually adjustable
Destacking feeder 3-080 with two feeder modules and additional C axis. Load capacity 60 kg
Hydraulic or pneumo-hydraulic marking station including double blank measurement. Centring nest can be integrated
Furnace roller conveyor (provided by customer)
Technical data
Cycle time | Up to 10 s |
Max. load capacity | 60 kg |
Blank length | 2500 mm |
Max. stack weight pallet | 6,000 kg |
Rotary axis of destacker | ± 135° |
Number of blanks per feeder | 2 |
Number of markings per blank | 4 |
Pressing force for marking | 120 kN |
Process time for marking | approx. 1.5 s |
Number of letters | up to 26 |
Press loading and unloading
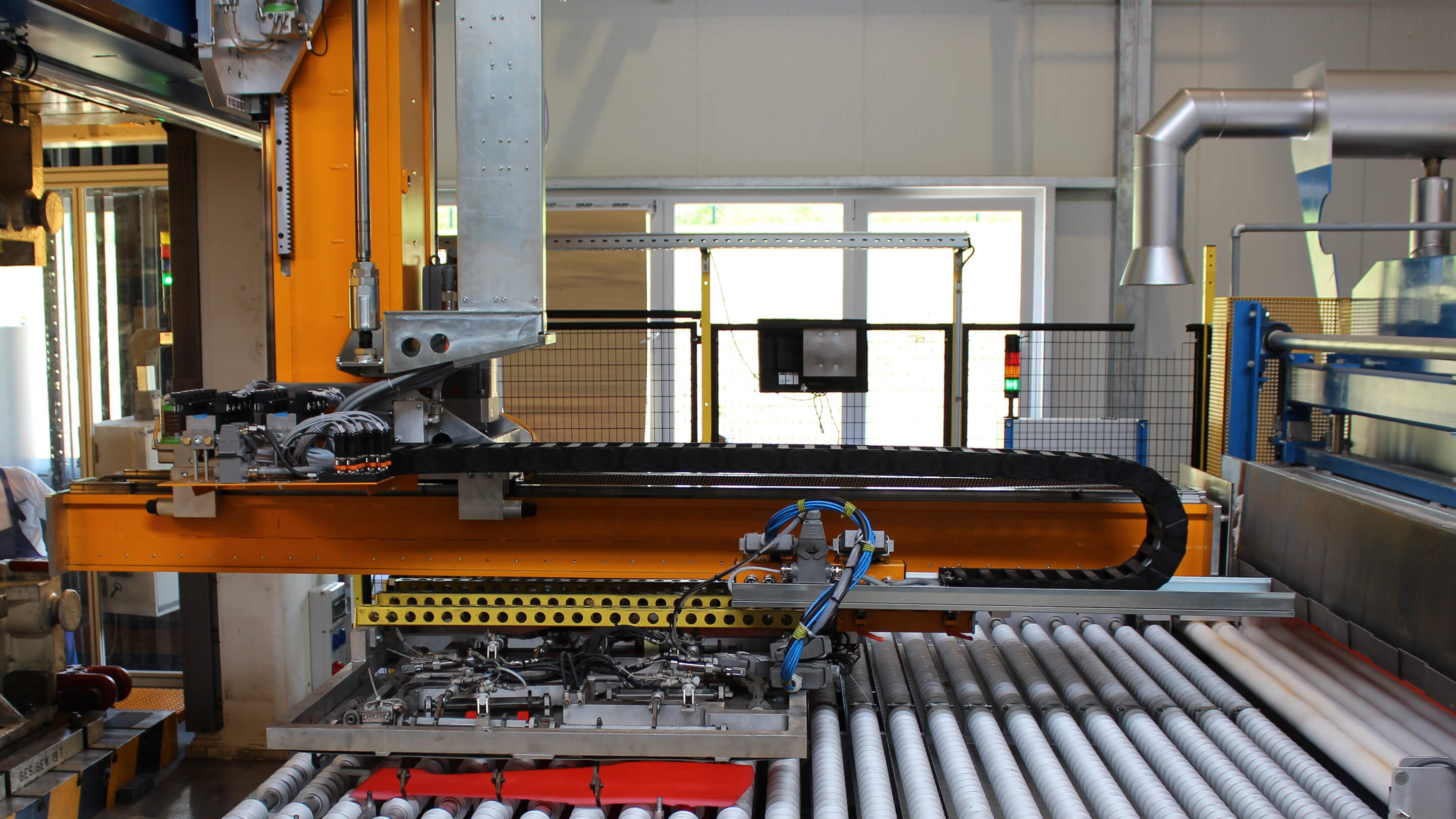
Feeder concept
- Press in furnace throughfeed direction
- Loading and unloading by one feeder each with load-bearing capacity of 200 kg or 120 kg
- Large toolings with heat shielding
- Achievable change time approx. 4 s
- Advantage: compact space and lower installed power
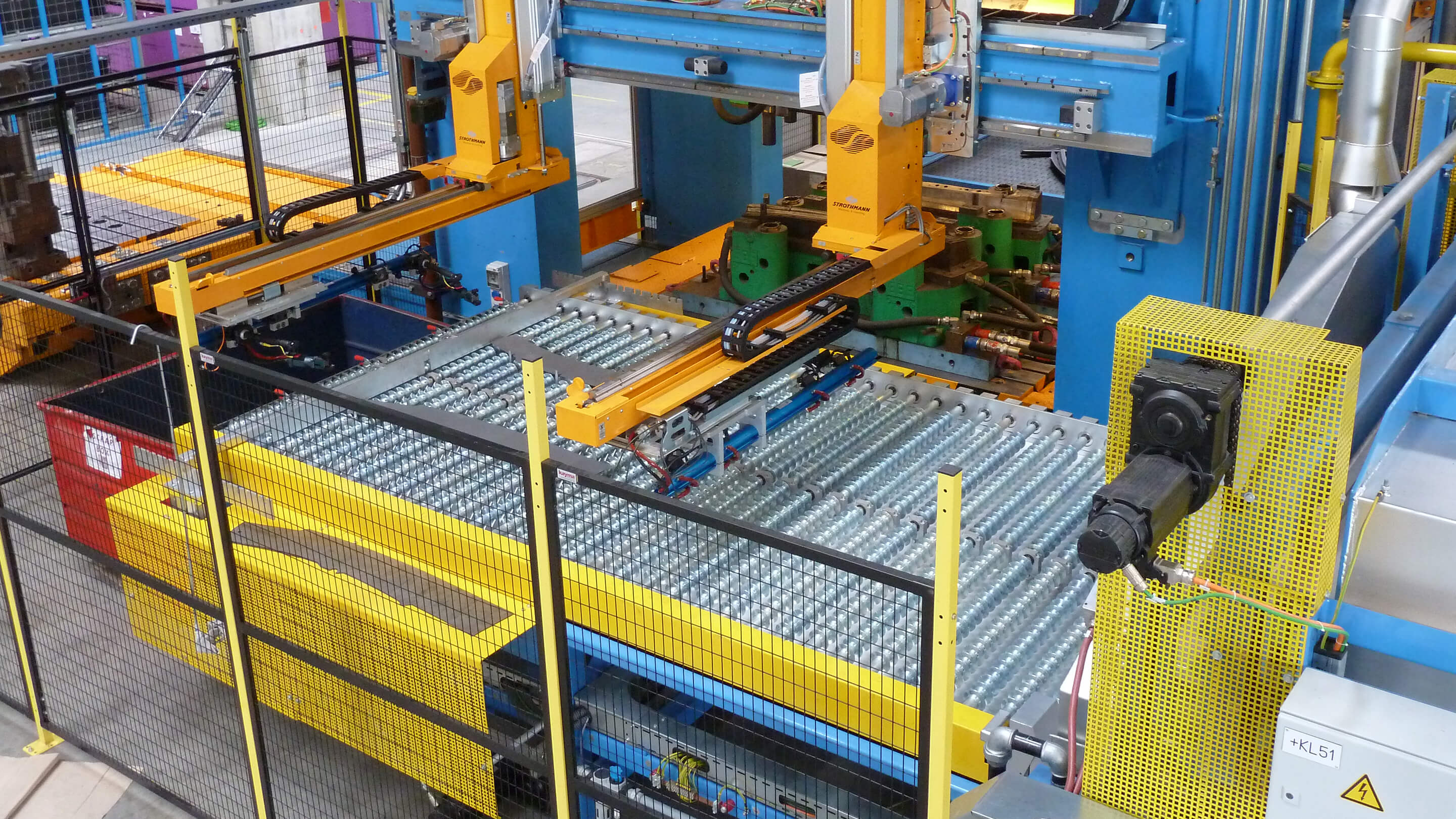
Transfer concept
- Press crosswise to furnace throughfeed direction
- Loading and unloading by two feeders each with 80 kg load-bearing capacity each
- Feeders wait in the press compartment next to the tools
- Achievable change time approx. 2.5 s
- Advantage: minimized cycle times
Feeder concept |
Transfer concept |
|||||
---|---|---|---|---|---|---|
Overall size |
1 |
2 |
S |
M |
L |
XL |
Automation unit |
3/200 (loader) |
3/200 |
3/040 |
3/040 |
3/080 |
3/080 |
max. stroke X |
3500 mm |
up to 6000 mm |
2500 mm |
3300 mm |
4000 mm |
4700 mm |
standard stroke Z |
1100 mm |
1100 mm |
700 mm |
700 mm |
800 mm |
800 mm |
Load-bearing capacity |
200 kg |
120 kg |
2 x 40 kg |
2 x 40 kg |
2 x 80 kg |
2 x 80 kg |
Achievable change time |
4 s |
4 … 4.5 s |
2.5 s |
2.5 s |
2.5 … 3 s |
3 s |