End of Line: Flexible solutions and scalable systems
At the End of Line, the fully formed workpieces are transported to manual or automatic stacking processes. SIEMPELKAMP Transport Systems automation systems separate the workpieces on the conveyor belts. In the simplest case, namely when using the FeederPlus 6neo, no additional systems may be necessary at all, depending on the customer’s requirements. This reduces the initial costs and service costs. Alternatively we offer additional shuttle systems, removal robots and the associated tooling changers.
System overview End of Line
End of Line: Structure
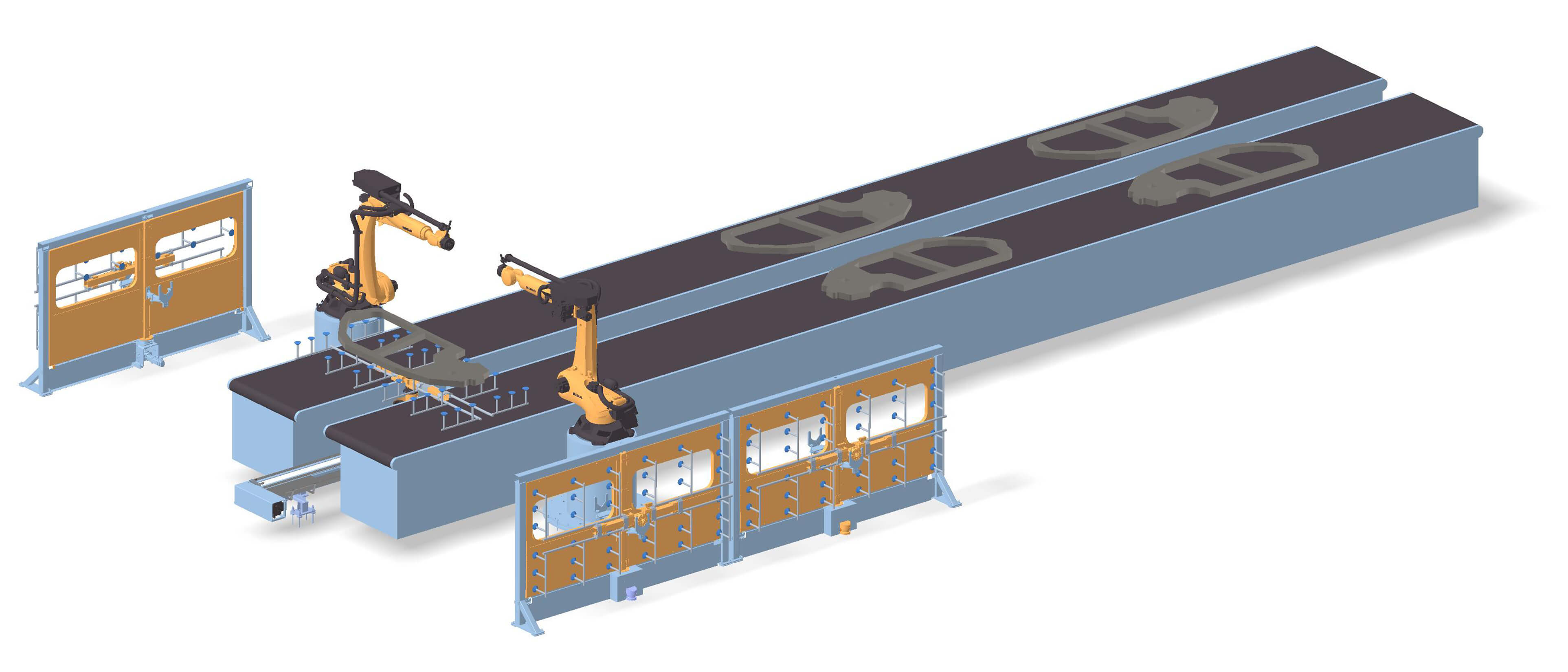
Shuttle for decoupling work areas of press automation and robots
Orientation robot for distributing workpieces on the conveyor belts
Tooling changing units for robots and shuttle, designed as revolving doors
Conveyor belts for transport to stacking process
Linear shuttle
The linear shuttle decouples the working areas of the automated unloading system of the final press and the orientation robot, thereby reducing lost time and even preventing collisions. It takes over the fully formed workpieces from the unloader of the final press and moves in the throughfeed direction to the transfer position to the orientation robots, which then place the workpieces on the conveyor belts. It is also possible to turn the workpieces around the C axis using the shuttle.
Operating modes | Transport Transport with rotation |
Max. performance | 17 SPM |
Load-bearing capacity | 120 kg |
Traversing path X | 2900 mm |
Rotation C | 180° (± 90°) |
Tooling interface | Tooling changing coupling on rotary axis. Entire tooling bar is changed |
Reversing shuttle
The reversing shuttle makes it possible to turn double parts around the B axis. For this purpose, the shuttle is equipped with a special double tooling. The unloader of the final press deposits the fully formed double part on the tooling nest of the shuttle. The shuttle reverses the part with a simultaneous up and down movement to prevent collisions of the workpiece with the conveyor belt and then deposits the part on the conveyor belts. Thanks to the double tooling, a free tooling nest is available to accommodate the next part immediately after the reversing process and no return stroke of the reversing axis is required. Conventional linear operation is also possible.
Operating modes |
Linear mode (no reversing) Reversing mode (no transport) |
Max. performance |
17 SPM |
Load-bearing capacity |
120 kg |
Traversing path X |
3000 mm |
Traversing path Z |
820 mm |
Rotation B |
180° (-0°, +180°) |
Tooling interface |
2 different interfaces for linear and reversing mode |
Tooling change
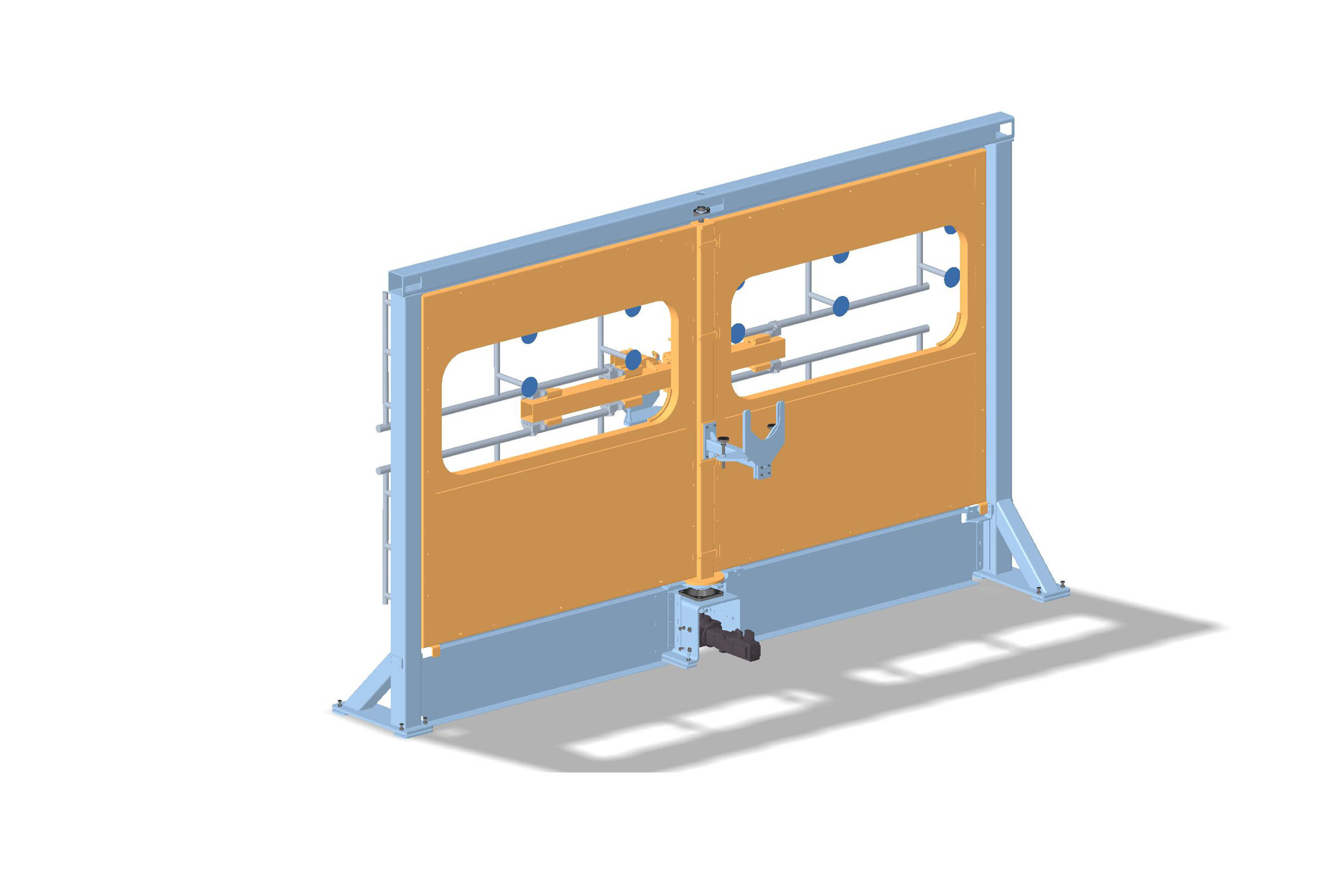
Tooling changing system - revolving door
This automatic tooling changing system is integrated in the noise insulation of the plant and is used for orientation robots and shuttles. It is equipped with two mountings for the tooling bars, one on each side of the door. This allows the robot to deposit its tooling in the protected area while the operator on the other side of the door has already prepared the new tooling. Laser scanners secure the pivot area of the door during the tooling change.
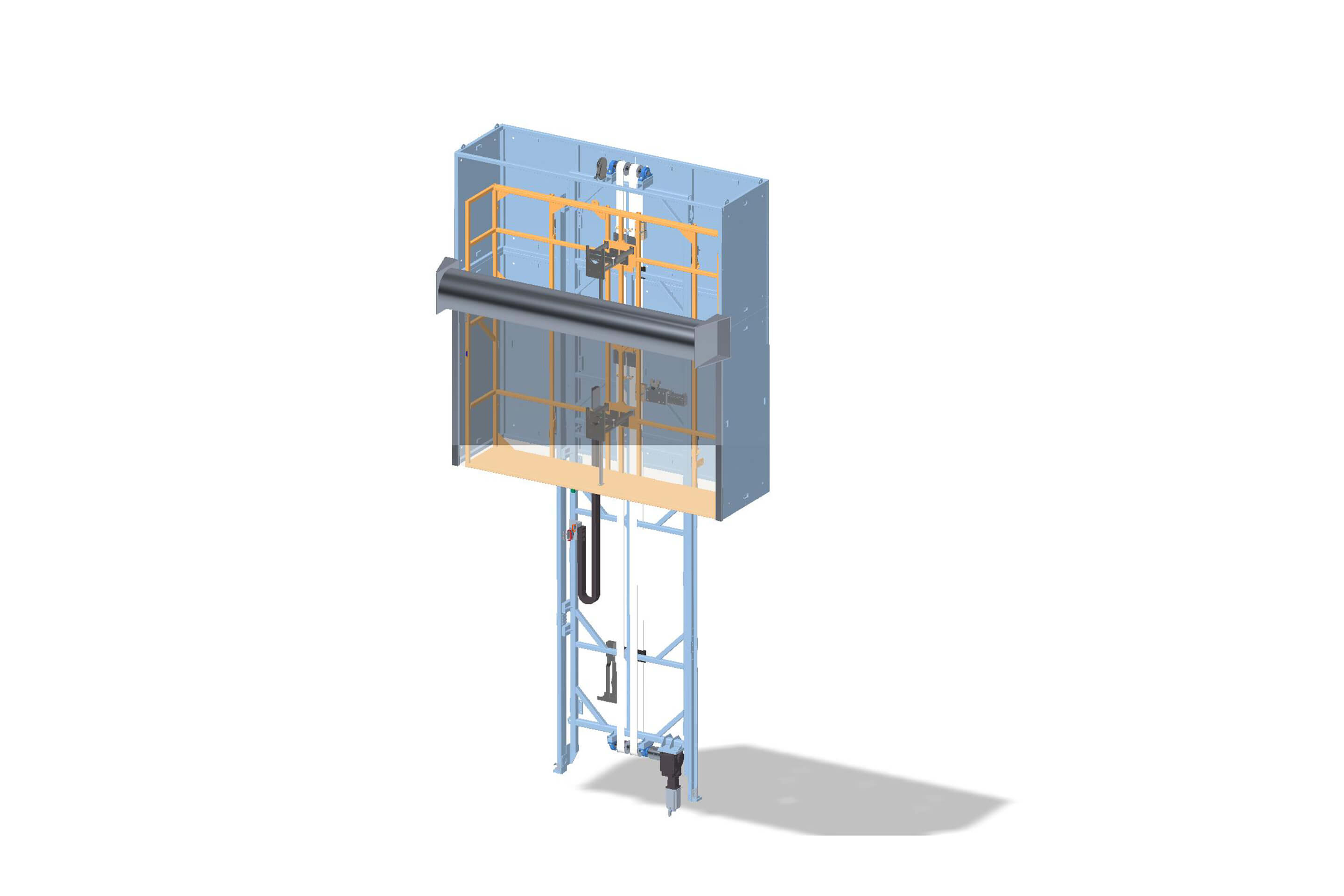
Tooling changing system for overhead applications
As an alternative, it is possible to transport toolings to the system roof using a lifting unit. The roof can then be used as storage area for the End-of-Line toolings. The lifting unit has two levels with one tooling mounting each, which are made accessible to the operator for set-up from the roof of the system through different parking positions of the units.