Automated Guided Vehicle (AGV):
The benchmark for Lean Production
uTrack is the Automated Guided Vehicle (AGV) system for demanding applications and the benchmark for lean production. The uTrack system is track-guided and has unbeatable advantages over conventional AGVs: e.g. efficient heavy-load transport, high-precision positioning, fleet accuracy and maintenance-free components. Due to these outstanding features and the extreme areas of applications, we call our AGV Ultra-Track or in short: uTrack.
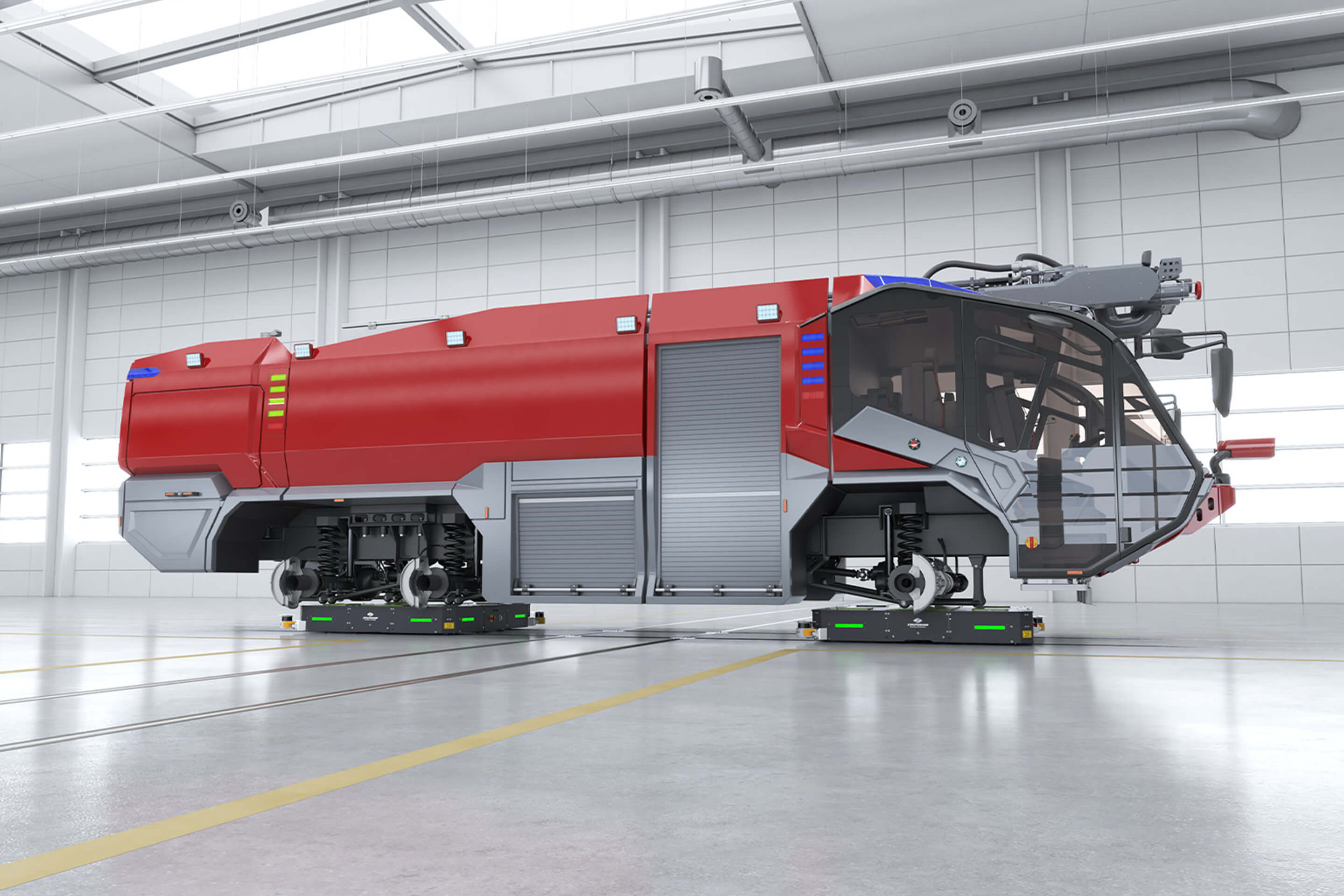
Ultra strong
Reliable and safe transport of products up to 200 t
uTrack is the heavy-duty AGV for automated material transport from 5 to 200 t: Due to the uTrack track guidance, even extremely long and wide loads can be moved safely. High load capacities can be realized regardless of the ground quality. Even large weight differences or the relocation of the material center of gravity have no effect on the positioning accuracy.
Ultra precise
Positioning and fleet repeat accuracy up to ±0.3 mm
The track guidance enables high-precision positioning and repeatability: consistently across the entire vehicle fleet. This unique feature enables optimal integration into automated processes and precise interaction with robots or machines. This reduces commissioning to a minimum. The uTrack track guidance eliminates lateral deviations, height tolerances or angular errors of the front and rear wheels.
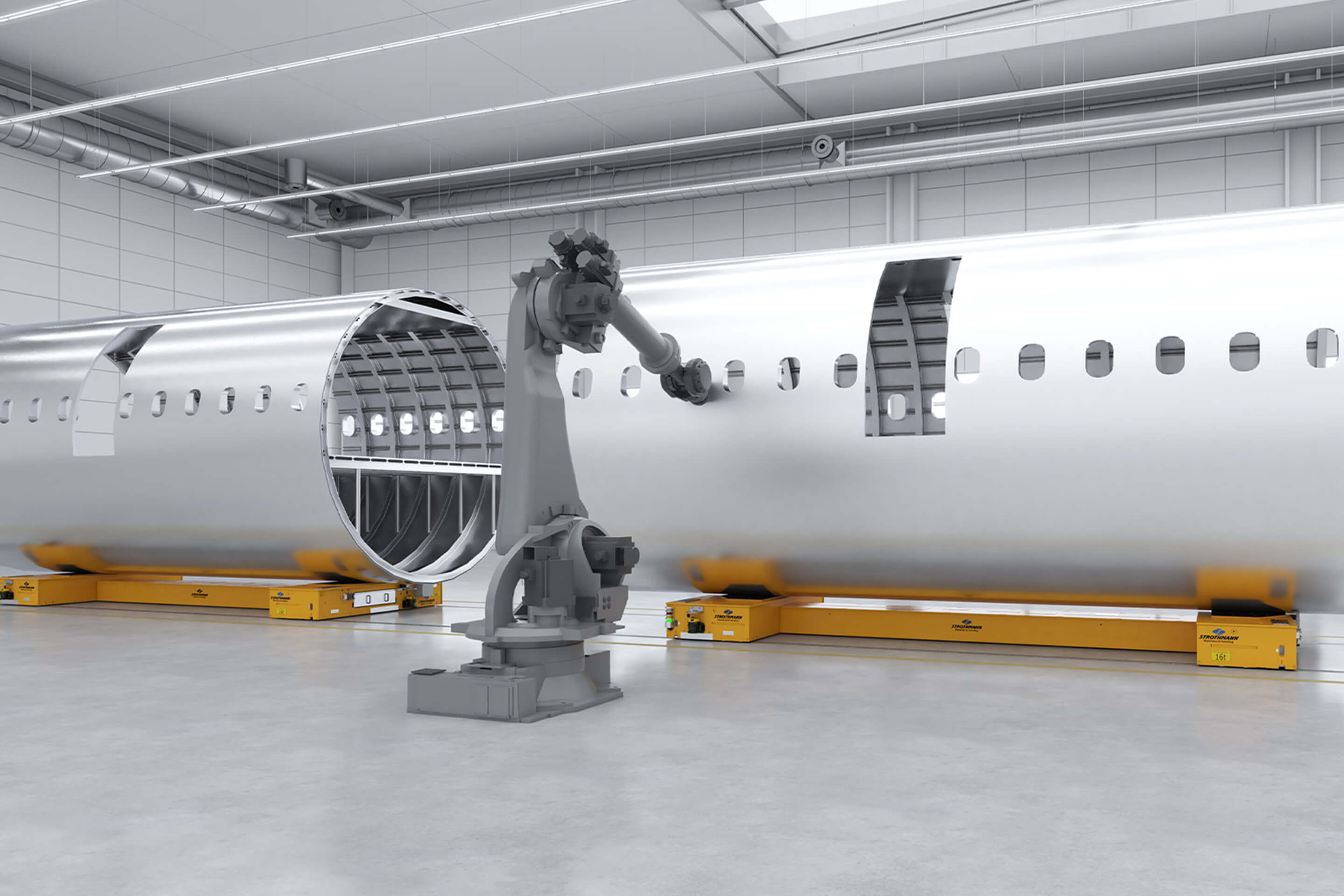
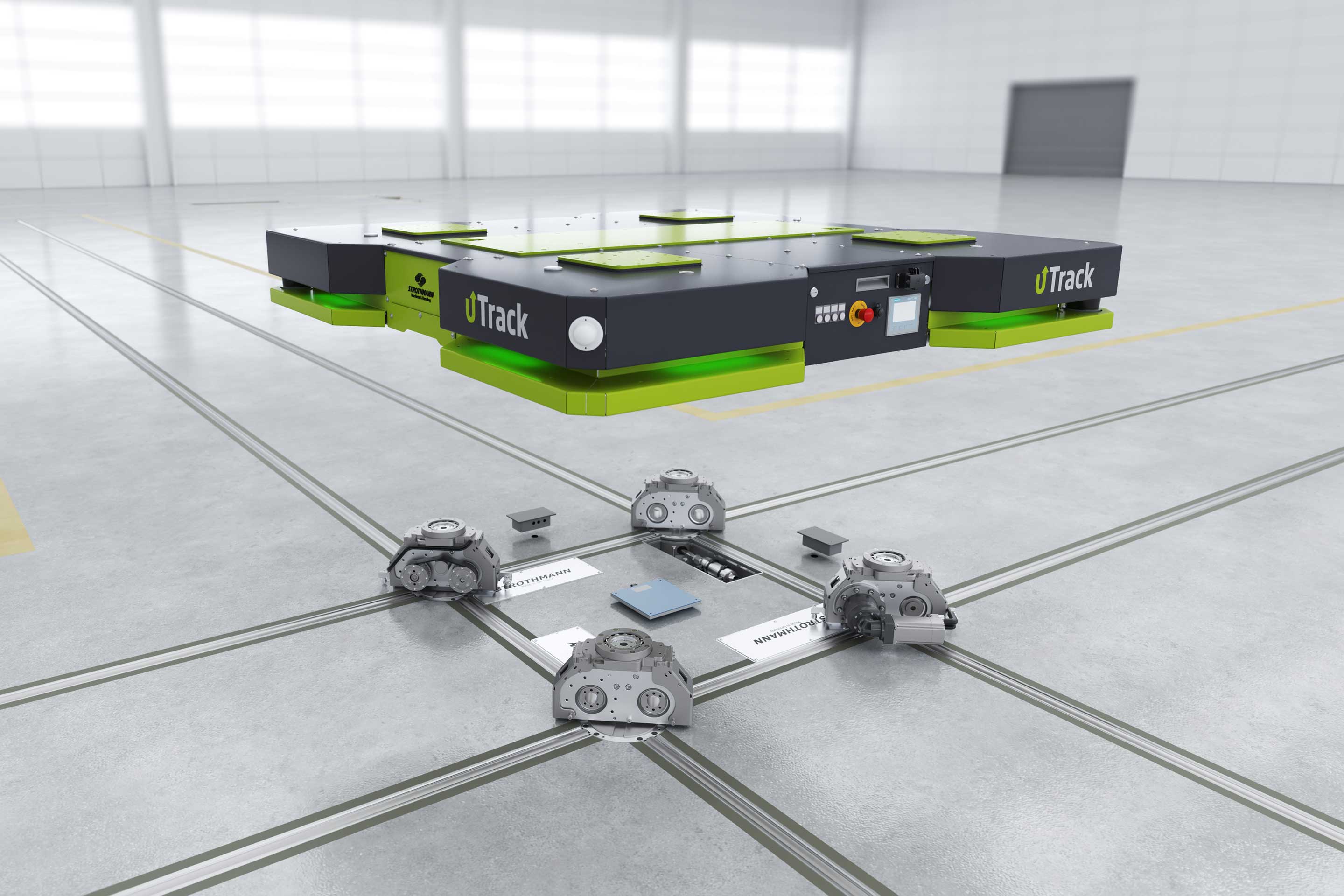
Ultra efficient
The lean system with low operating costs
The lean design and the use of energy-efficient components make the uTrack system particularly economical and sustainable. Due to the minimal rolling resistance between the steel wheel and the steel rail, only low drive power is required to move large loads. Unlike conventional AGVs, there are no ruts in the production line and hall transitions or floor joints remain intact. Maximum productivity is offered by the integrated emergency concept: in the event of a system or power failure, uTrack keeps on working.
Ultra compact
The flattest AGV system in its performance class with a total height of 260 mm
The uTrack track guiding system offers extremely high payload in an extremely small space. The result is an ultra-compact AGV with a low total height. Only 260 mm for an AGV with a capacity of up to 40 t. uTrack improves the ergonomic situation for work at and on the transported product, offering plenty of space around the AGV and making it possible to climb on and off the cart without any additional aids.
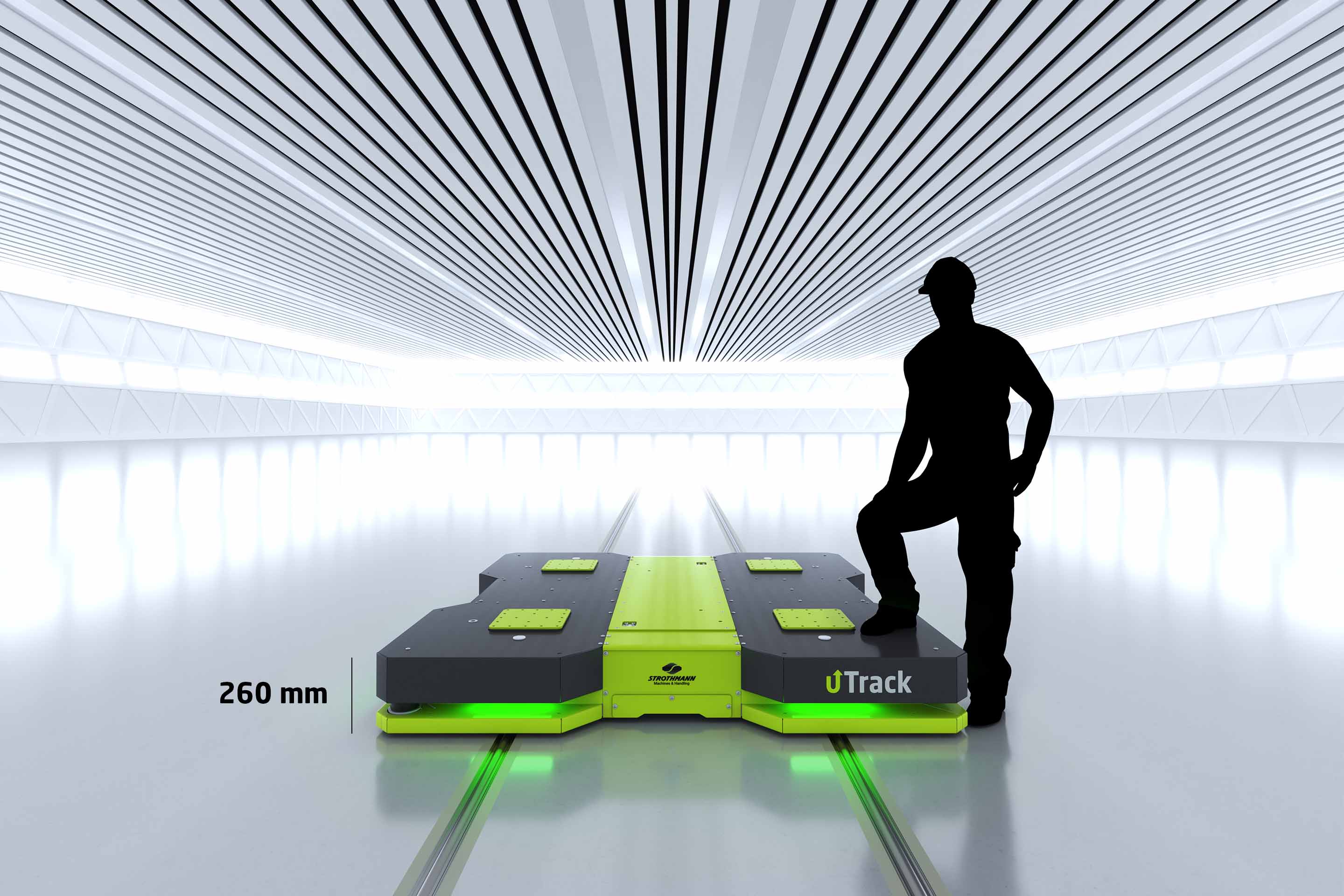
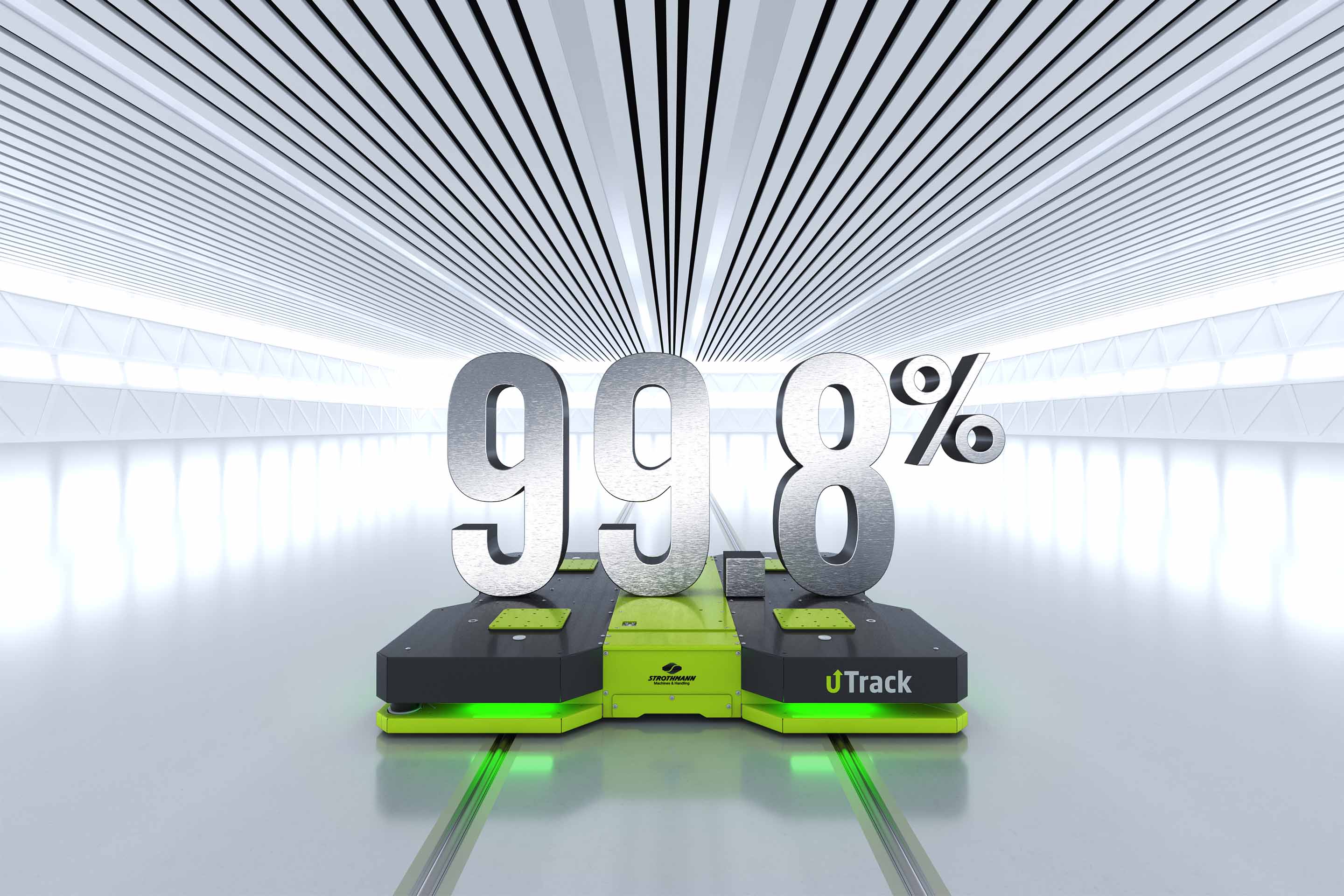
Ultra available
Minimized downtimes through maximized production reliability
uTrack is the optimal AGV for top production reliability. The reasons: An extreme robust technology in almost every production environment and an emergency concept in each AGV is standard. If a cart experiences unplanned downtime, operation can be continued manually in emergency mode. This means the product can remain on the cart and downtimes are minimized.
UTrack’s Leading edge:
Advantages over conventional Automated Guided Vehicles (AGV)
System comparison of Forum-AGV
Reduction of maintenance and energy costs (TCO)
- no component replacement due to abrasion
- no repairs to drive ways
- no service and maintenance stations
- no subsequent teaching
- no downtime due to loss of positioning
- reduced energy costs due to minimal friction
- low acquisition costs compared to conventional AGVs
Change of orientation
- only when changing direction combined with a change of orientation is needed, the uTrack system requires more effort
Autonomous driving
- track guidance is an efficient organizational and planning tool
- the better the production planning, the less flexibility is needed
- the uTrack system can be flexibly retrofitted and extended
Precise load transport up to 200 t
- high load capacities, regardless of the floor quality
- no effect of weight differences and center of gravity shifts on transport or transfer
- no height tolerances, e.g. in high-bay warehouses
- no inclination at the wheel/floor contact points
- no change in long-term use: floor quality, wear of wheels
- no angular deviations in the guidance of extremely large loads
Precise track guidance and positioning
- repeatable positioning and repetitive accuracies up to ±0.3 mm
- no lateral deviations
- no height tolerances
- no angular errors of front and rear wheels
- no separate protection of objects, e.g. storage systems
- no separate space requirement for safety zones
Precise fleet accuracy
- Highest fleet repeatability
- minimization of commissioning
- no individual teaching of single vehicles
Low overall height
- only 260 mm construction height for loads up to 40 t with change of direction
- even flatter overall construction heights without change of direction
- ergonomic assembly heights for employees
- compact carriage geometry for best accessibility
Maintenance-free system
- alle uTrack Komponenten sind wartungsfrei
- no maintenance or replacement of wheelsets
- no redundant drives
- no stocking of spare parts
- no open space for maintenance work
- no need for reserve vehicles
Reduction of required space
- no safety surfaces due to imprecise movements
- no breakout of the trolley
- no areas for maintenance work
- no areas for reserve vehicles
- minimal space requirement when changing direction
Highest availability and security
- maintenance-free components
- high reliability
- integrated emergency strategy by disengaging the trolleys
- safe and precise positioning
- no breakout of the trolley
- safe travel on water and oil
- no problems with metallic particles and chips
No floor abrasion
- no point loading due to the wheels
- no ruts in the hall floor
- no floor maintenance in the area of the track-guided AGVs
- for example forklifts and pallet trucks can easily drive over the RoundTrack
- best possible safety at work by avoiding tripping hazards
High energy efficiency
- minimal rolling resistance due to steel on steel (wheel on RoundTrack)
- minimum drive power required
- low power for moving heavy and large loads
Reduction of total costs (TCO*)
On the road to success with uTrack. Benefit from the economic advantages of the uTrack system. Compared to other AGVs, uTrack already scores with the lower acquisition costs. Further savings result from the reduction of maintenance and energy costs: e.g. no wear-related component replacement is necessary. Repairs to the RoundTracks are not necessary. In addition, no service or maintenance stations are required. Another plus point: downtimes due to the loss of the carriages position are eliminated. This means that no subsequent teaching of the carriages is necessary.
*TCO: Total Cost of Ownership
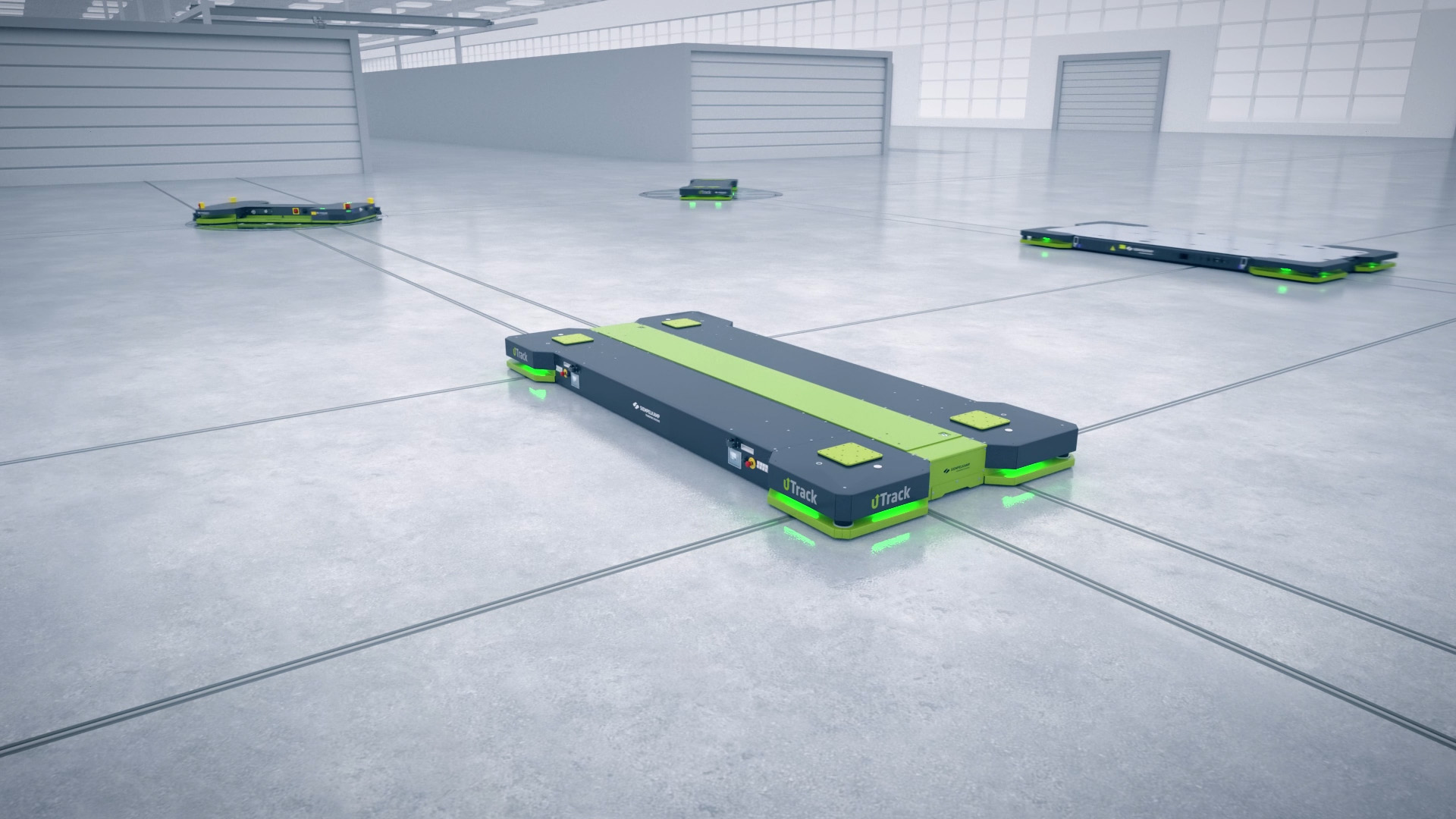
UTrack: The game-changing AGV built for the future
The global competition is intensifying. The demand for highly efficient production systems has never been greater. Companies are facing the challenges of lean processes, maximum availability, and future-proof solutions.
Discover uTrack now – the ideal AGV for large and heavy-load manufacturing.
UTrack’s system
components: robust and reliable
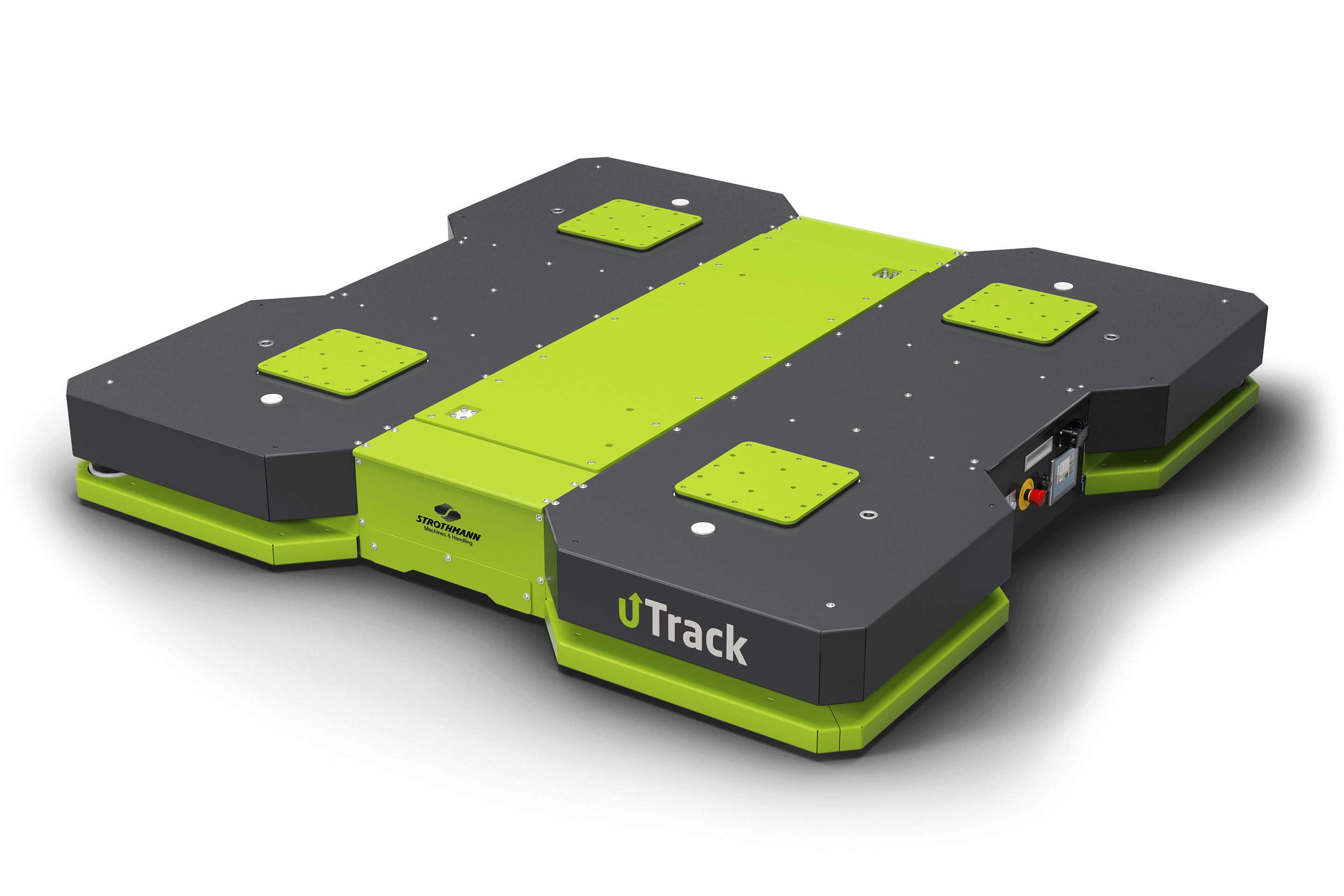
The uTrack transport cart
The cart transports products up to 200 t automatically and with high precision. The chassis design can be individually adapted to the requirements. All system components are maintenance-free and designed for long-lasting use. The energy supply of the uTrack transport cart can be flexibly selected: battery or induction drive.
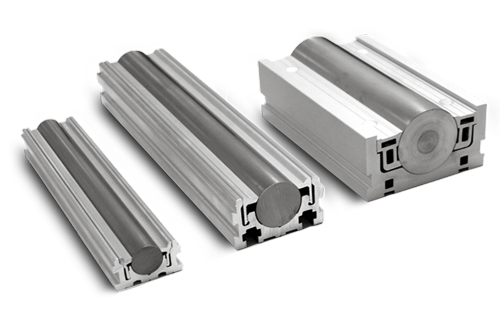
The uTrack track guidance
The RoundTrack is the basis for the exact and safe guidance of the transport cart. It is installed in the floor and can be driven over by any vehicle. Turning and lifting devices allow the AGV to change direction easily. This means that any position can be reached at the site of operation. The hall floor remains undamaged.
UTrack’s areas of application
from universal to extreme
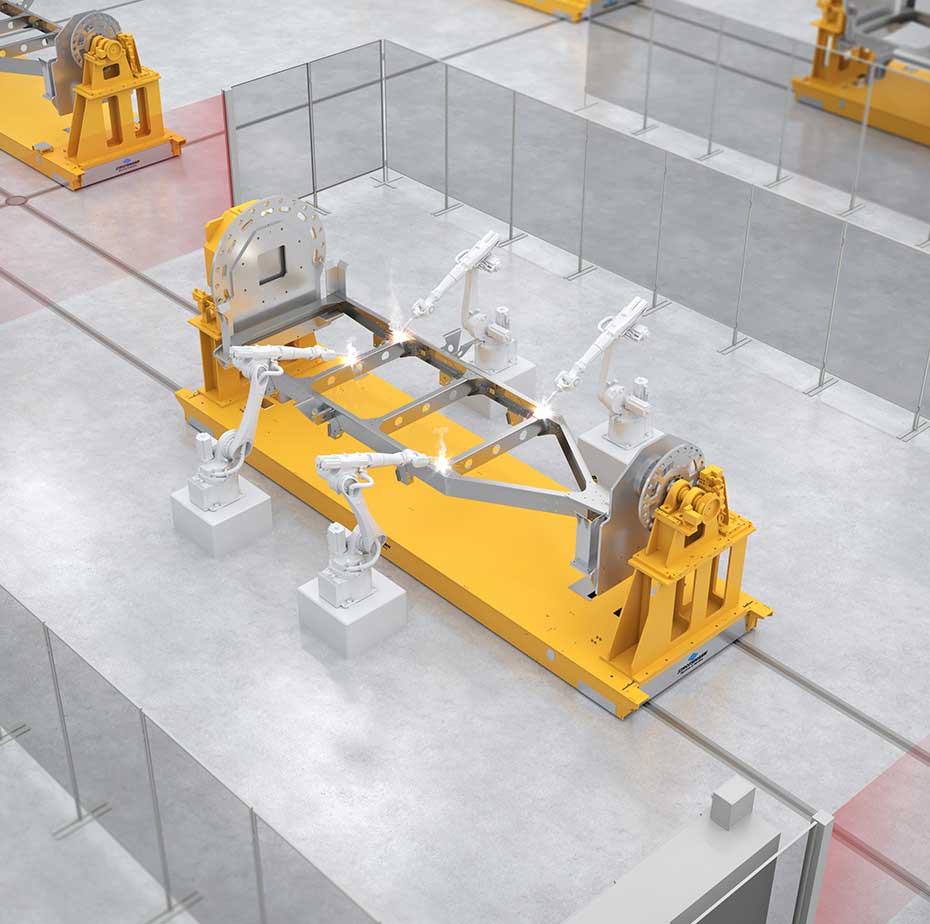
Joining: Accurate positioning and repeatability is necessary for joining components. This applies to processes such as welding parts, applying various substances such as sealants or adhesives to parts, or measuring parts in quality inspection stations.
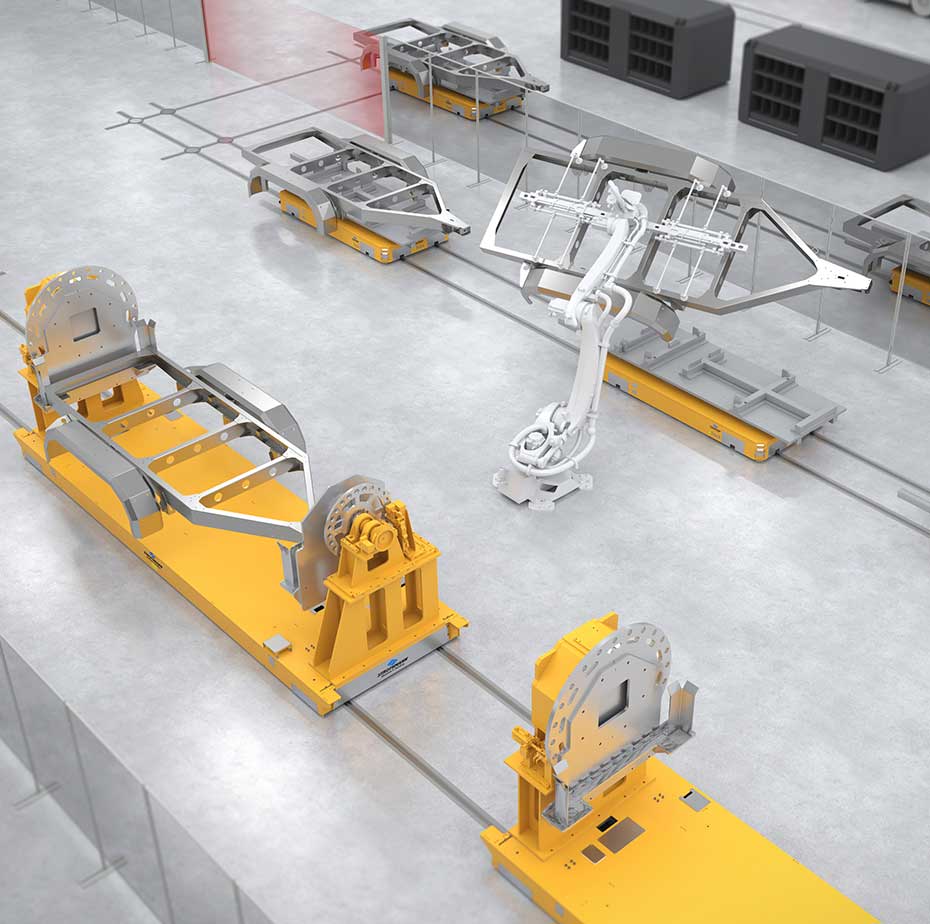
Transfer: Several transfer points are necessary in production. In order not to lose productivity, this step must be completed as quickly as possible. In addition, other forces that can act on the carriage during transfer must be safely compensated.
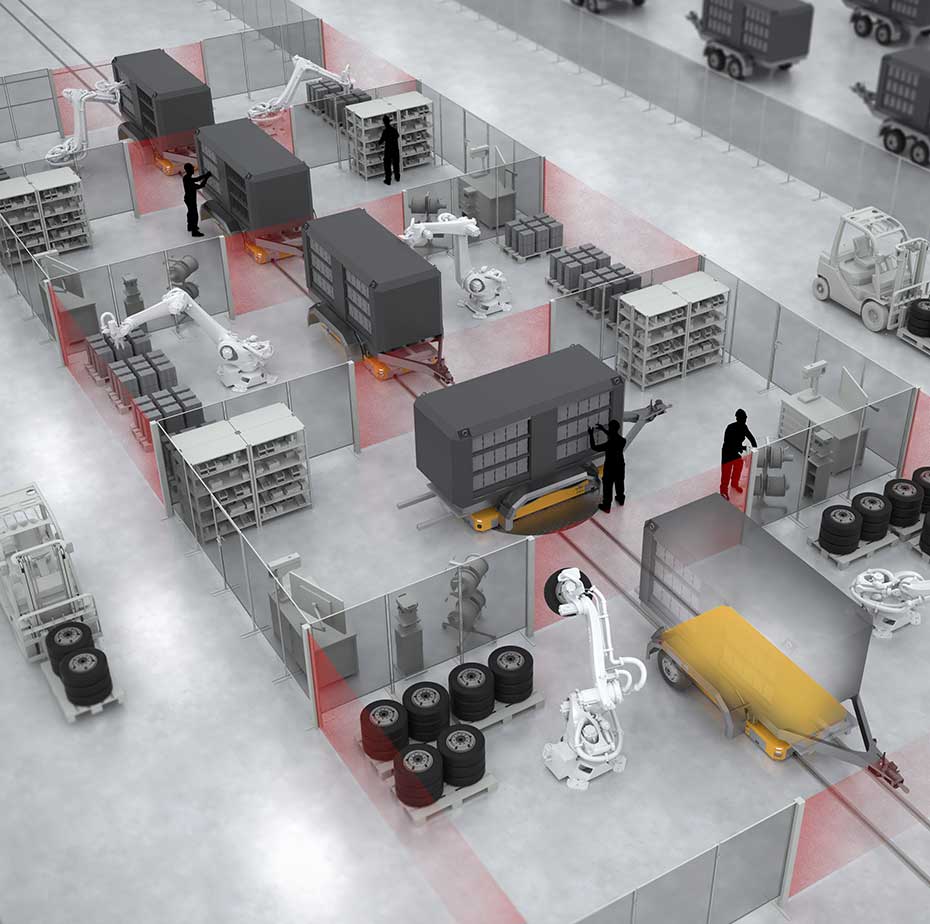
Assembly: Human-machine interaction in assembly lines is becoming increasingly important. Simple and monotonous assembly tasks are increasingly being taken over by robots. At the same time, products are becoming increasingly complex.
FAQ: Frequently Asked Questions about Automated Guided Vehicles (AGV)
Automated guided vehicles (AGVs) are in-plant, floor-based conveyor systems with automatically controlled vehicles (AGVs) whose primary task is to transport materials, but not people. They are used inside and outside production buildings and essentially consist of
- one or more driverless transport vehicles,
- a control system,
- equipment for determining location and recording the situation,
- data transmission equipment, and
- infrastructure and peripheral equipment.
(Source: VDI-Richtlinie VDI 2510 „Fahrerlose Transportsysteme“; Beuth-Verlag, Berlin, S. 6 f.)
There are many possible applications for AGVs in the areas of production, distribution and services. As a result of the diversity of areas of application and tasks, there are in principle no design limitations for AGVs. The majority of systems implemented to date can be characterized by the following overview:
Number of AGVs per system: one to several hundred
Load capacity of an AGV: a few kg to over 50 t
Travel speed: typically 1 m/s, but deviating values are also possible
Driving course length: a few m to over 10 km
Number of stations: unlimited (load change and work stations)
System control: manual to fully automatic, stand-alone or integrated in complex material flow systems
Operating time: sporadic to 24/7
Drive concept: electric motor driven, with or without battery combustion engine driven
Guided AGVs follow a defined route. For example, through rails embedded in the ground, transponders and other guidance systems. Autonomous AGVs, on the other hand, are equipped with additional sensor technology and navigation, which enable them to detect their surroundings, recognize obstacles and independently select a route.
With rail-guided AGVs, high load capacities can be realized regardless of the ground quality. Even large differences in weight or the shifting of the material's center of gravity have no effect. This enables efficient material handling of large and heavy products. These systems are referred to as heavy-duty AGVs. In addition, rail guidance ensures high precision. High precision is necessary for interaction with other machines for automated processes, as repeatability and small tolerances are required in this area.
Track guided vehicles (AGVs) offer several advantages, especially in certain applications and environments.
Efficient and reliable process: Guided AGVs can travel precisely and predictably along a predefined route. Fixed guidance on rails, magnetic guidance systems or floor markings enables accurate movement and positioning. This is especially necessary in environments where efficiency and availability are important, such as assembly lines and production facilities.
High load capacity: An automated guided vehicle system is ideal for transporting heavy or large products. Track-guided AGVs on rails are particularly preferred when transporting heavy loads (heavy-duty AGVs). The rail guidance helps to ensure stability and safety during transport.
Easy installation: Track guided systems usually require relatively simple installation. The rails, guide magnets or floor markers can be anchored into the infrastructure or placed on the floor. This facilitates system implementation and allows for quick start-up.
Cost efficiency: Track guided, automated transport systems are maximally efficient. They travel along a defined route, optimizing the availability of the AGV and thus improving the productivity of the entire production process.
Safety: Due to the stable guidance, track-guided AGVs offer increased safety in production. Since they cannot deviate from the predefined route, the risk of downtime due to unplanned stops or detours is reduced. This is particularly relevant in the final assembly area, as this is where most interaction with all other transport processes takes place.
Track guided AGVs are best suited for lean production. The advantages of lean production are cost savings, high productivity, quality and flexibility. This is achieved through lean processes and high utilization of machines and equipment. In particular, transport and waiting times are reduced to a minimum, as they are considered wasteful by definition and have a negative impact on the principle of flow production.
Automated guided vehicles automate transport and can ensure consistently high availability. Especially track guided AGVs have the advantage of optimal flexibility. Only routes that effectively map the production process are defined and do not allow any further deviations.
Autonomous transport systems offer maximum freedom and flexibility. In the AGV sector, these are currently referred to on the market as autonomous mobile robots (AMR). Depending on the degree of autonomy, they can support lean production by optimizing transport processes independently.
For lean production in production, AMR are rather unsuitable, because the autonomous transport leads to more transport and downtime due to additional flexibility instead of less. The autonomous driving around of obstacles can be mentioned here as a particular negative example. In addition, the operating costs for an AMR are many times higher than for a classic track-guided AGV.
A rail-guided AGV offers maximum efficiency through maximum production reliability. It is the simplest way to implement an automated guided vehicle system and offers the best availability with optimum flexibility. Especially as a heavy duty AGV for loads over 2,000 kg, it has unbeatable advantages e.g. in energy efficiency, compactness and safety. In addition, the total cost of ownership (TCO) over the planned system lifetime is the lowest.
AGV Automated Guided Vehicle
AMR Autonomous Mobile Robots (Autonomous Transport Systems)