UTrack application areas: from AGV Interaction to AGV final assembly line
The SIEMPELKAMP automated guided vehicles have been in use since 2004. Due to the many years of experience and the high system availability, customers worldwide trust in uTrack. The AGV offers numerous advantages that enable flexible use in different industries. Especially in areas of application where large and heavy loads, high accuracy or interaction with other machines is required, uTrack is unrivaled.
ultra strong: reliable transport of large and heavy loads
ultra precise: minimum tolerances and maximum positioning accuracy
ultra efficient: maintenance-free system and low operating costs
ultra safe: maximum safety for people and objects
ultra robust: easy movement in case of malfunction for highest availability
Ultra strong: AGV for large and heavy products in pre- and final assembly line
The optimal application for the uTrack system is the transport of heavy products from 5 - 200 t in the area of pre- and final assembly. Application examples
- Commercial vehicles
- Construction and agricultural machinery
- Aircraft industry
- Manufacturing systems
The uTrack lead
- reliable transport of heavy and large-volume loads
- highest safety for persons and objects
- high availability
- low operating costs
- integrated emergency strategy
Agriculture
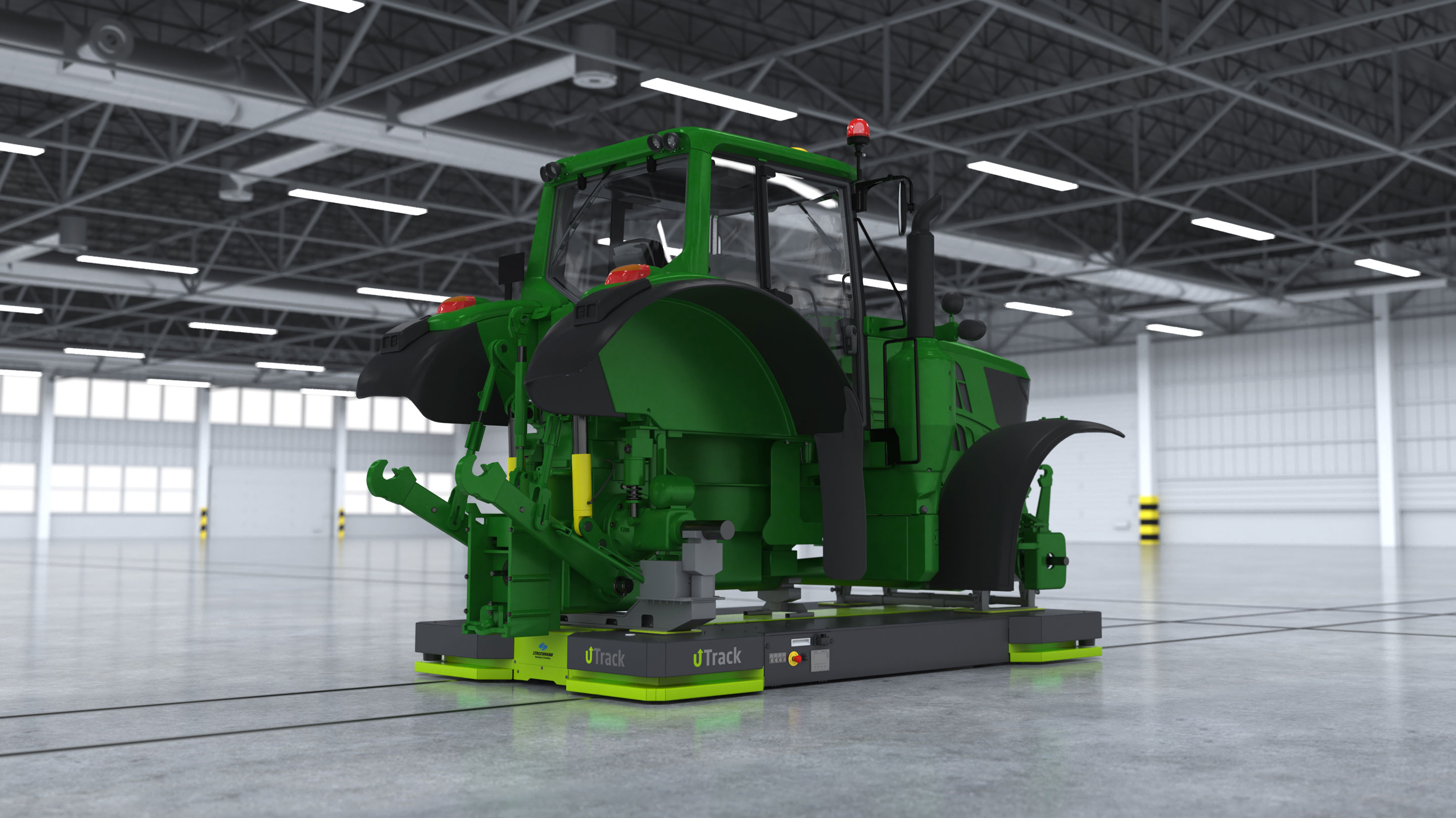
Construction industry
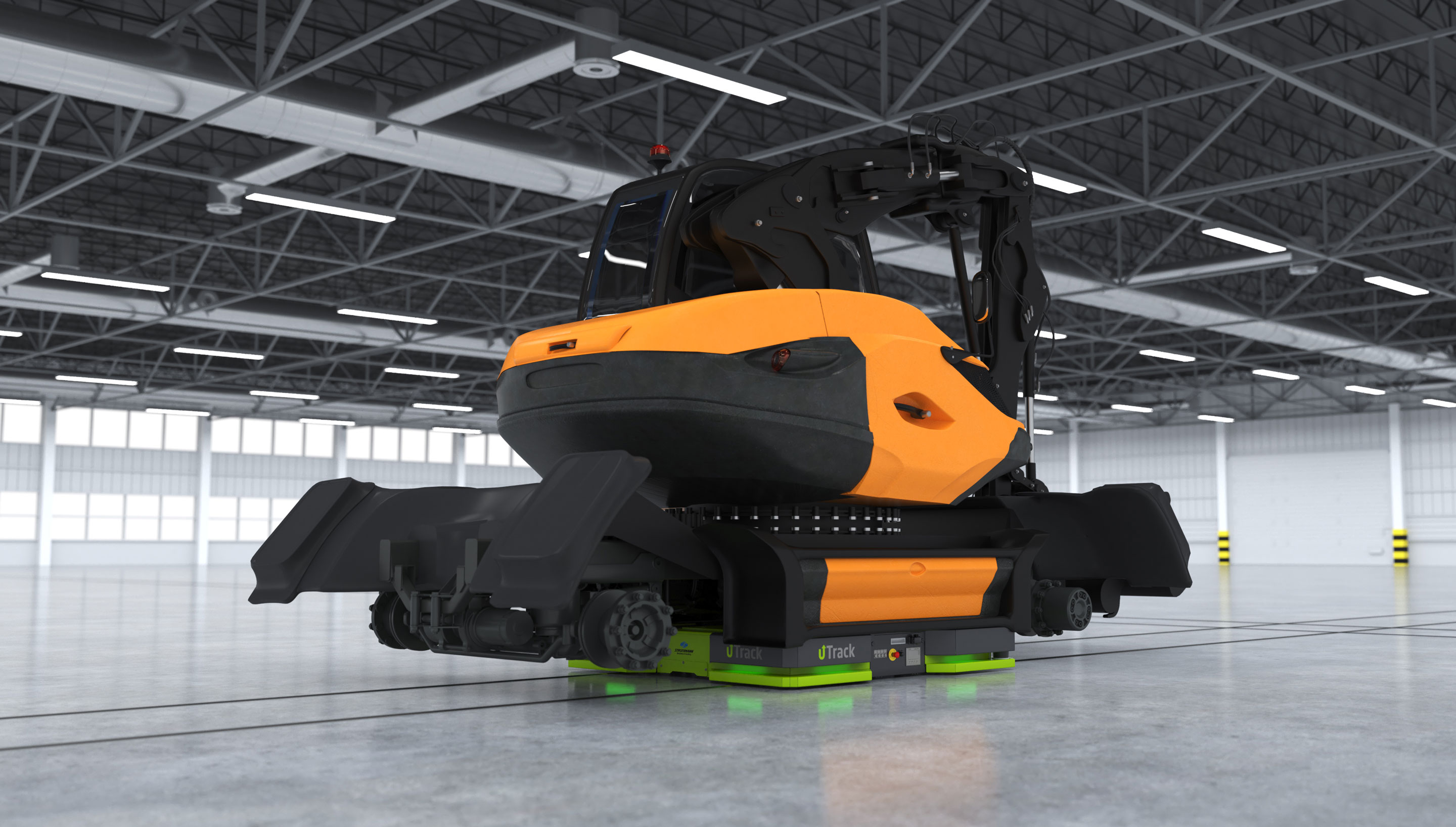
Automotive
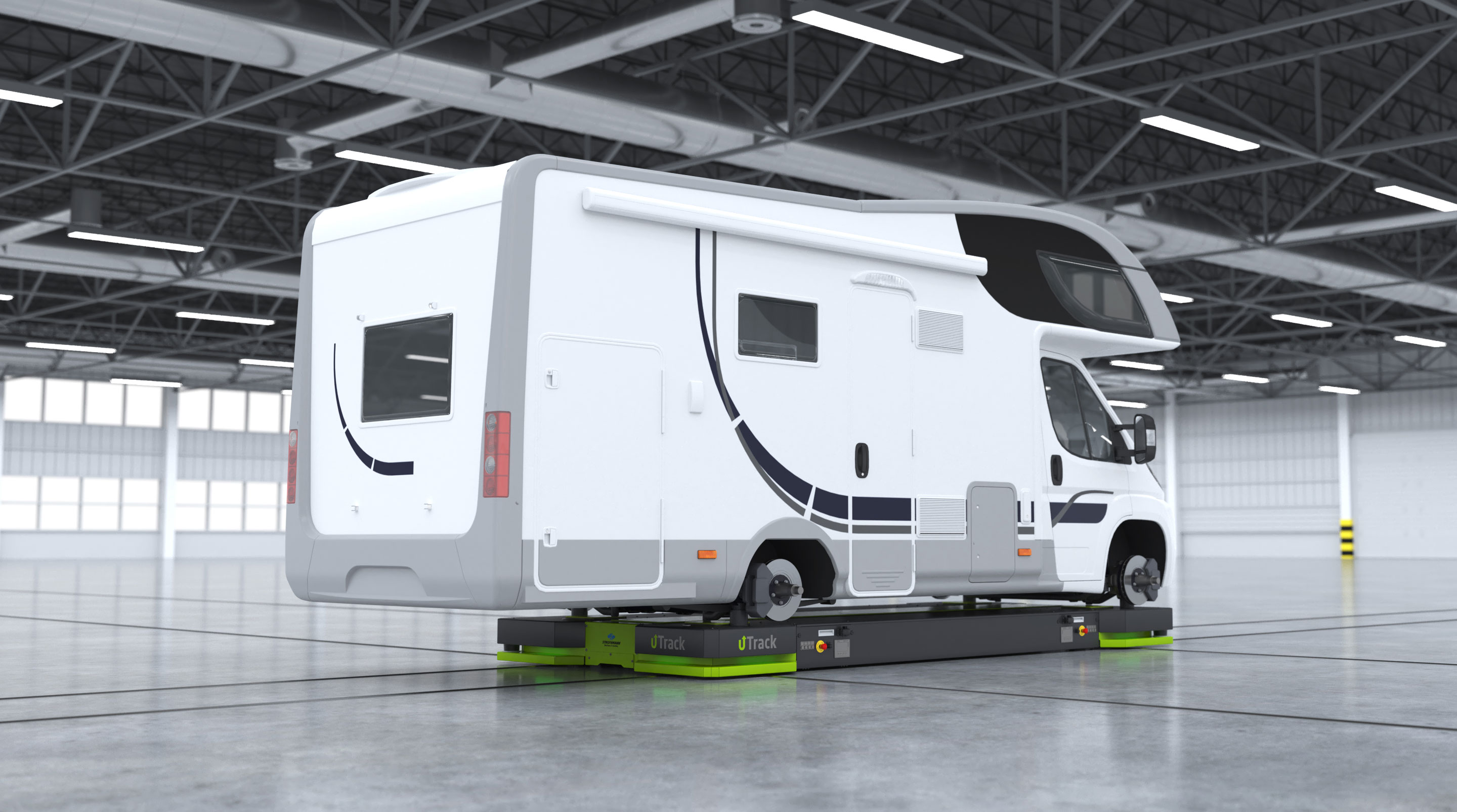
Commercial vehicles
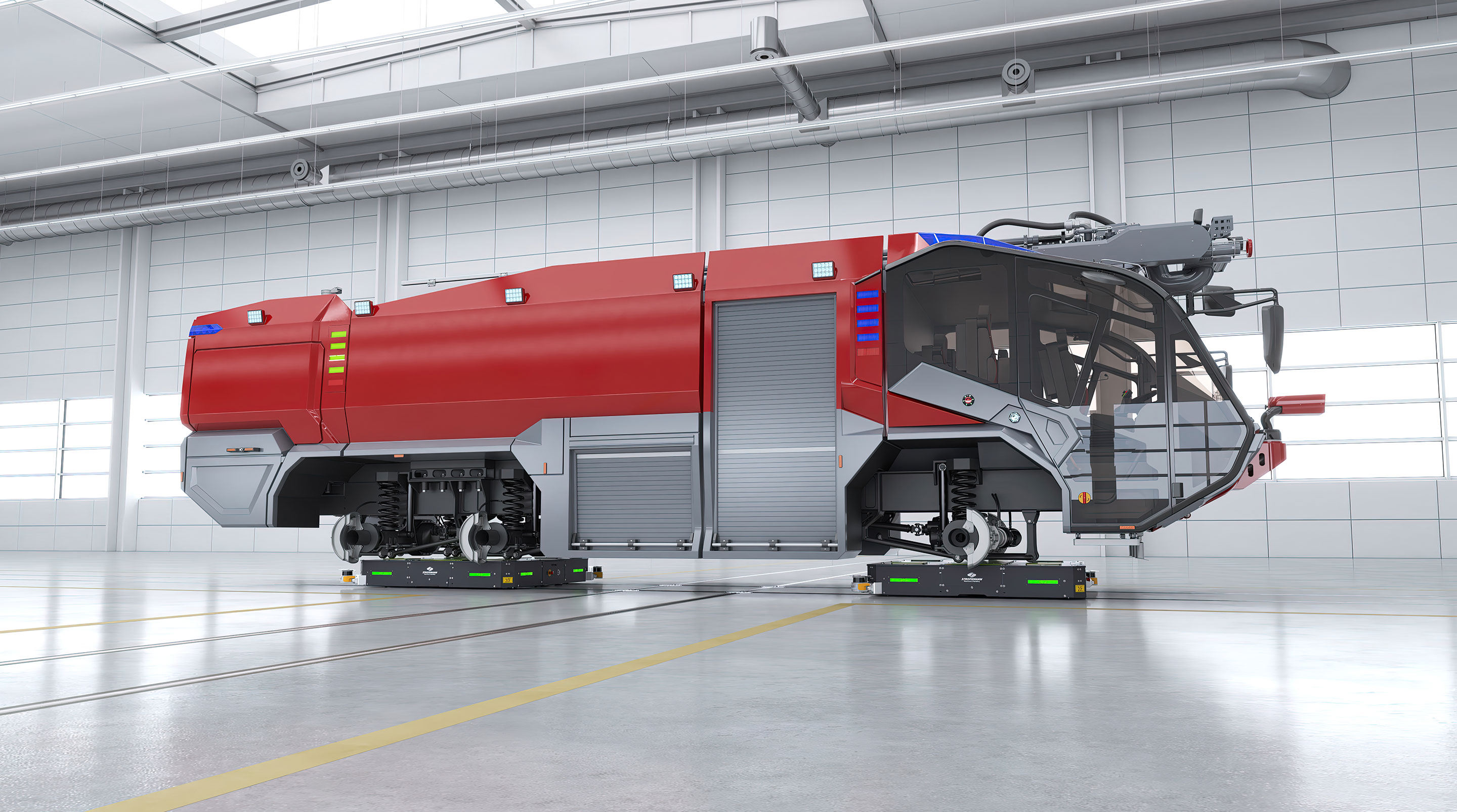
Ultra precise: AGV interaction with high requirements on position and repeat accuracy
Due to the very high repeatability of the uTrack system, interactions with other machines and complex systems can be realized with the highest precision. Application examples:
- Machining centers
- Welding and riveting robots
- Stacking stations
- Lifting tables
The uTrack advantage
- easy integration into automated processes
- precise positioning and repeat accuracy
- interaction with stationary equipment
- highest safety for persons and objects
- highest availability
- low operating costs
Joining
Accurate positioning and repeatability is necessary for joining components. This applies to processes such as welding parts, applying various substances such as sealants or adhesives to parts, or measuring parts in quality inspection stations.
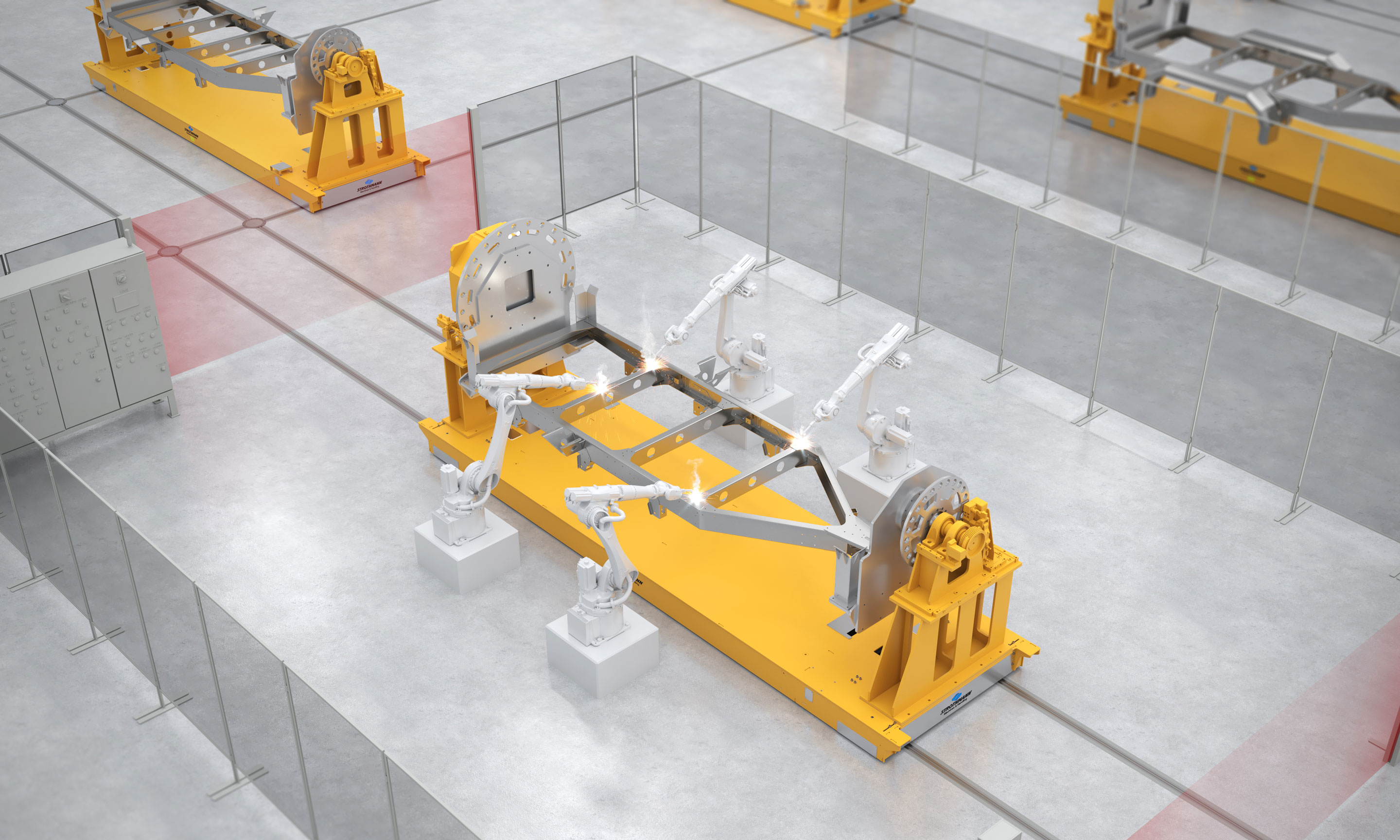
Complete integration into the safety concept of the overall plant.
Various additional functions such as turning and lifting are possible.
Interaction with various robot types.
Individual product pickup on the cart surface.
Transfer
Several transfer points are necessary in production. In order not to lose productivity, this step must be completed as quickly as possible. In addition, other forces that can act on the carriage during transfer must be safely compensated.
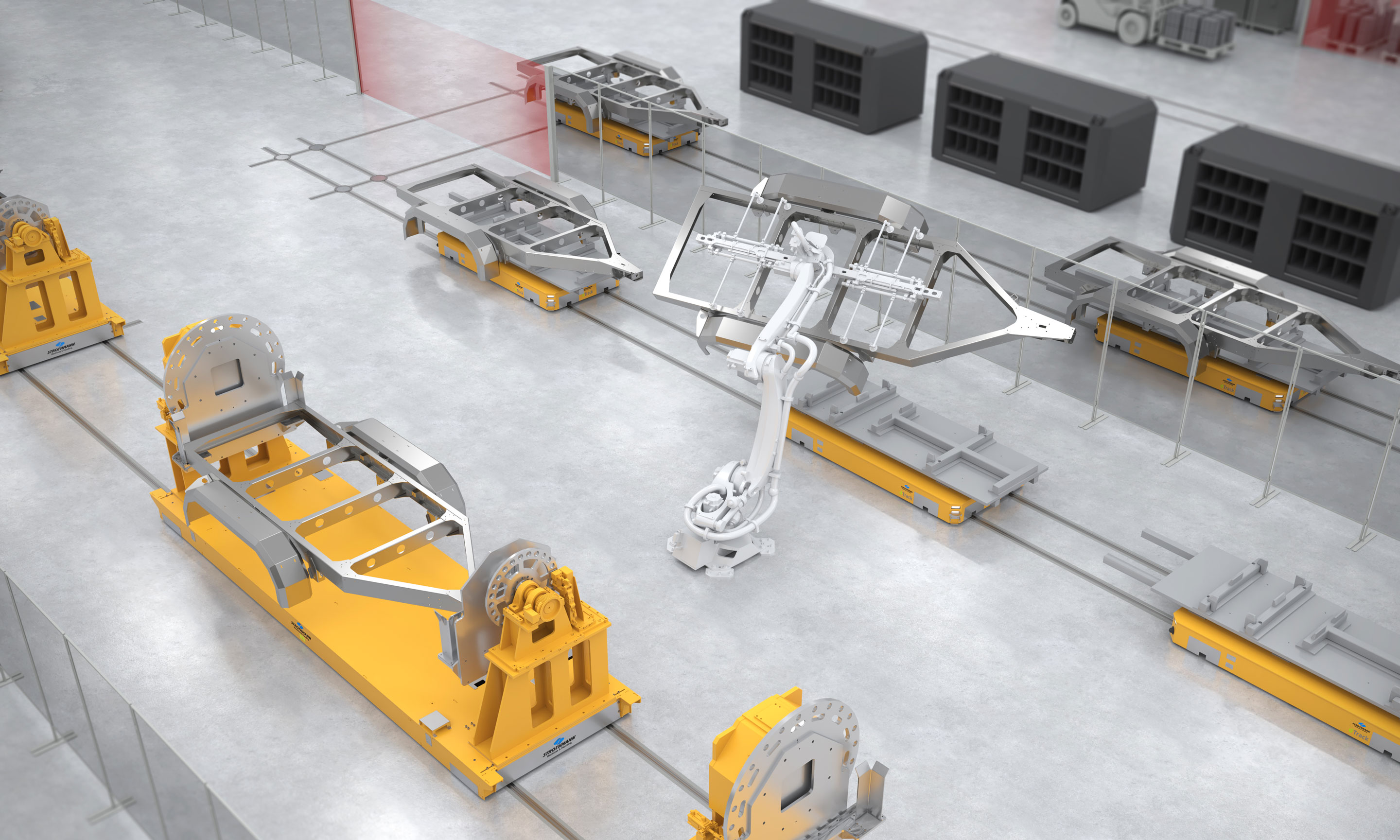
The transfer can be carried out by another system such as a P&F conveyor or a crane.
Due to the precise tracking, the transfer process can be carried out in a small space.
Assembly
Human-machine interaction in assembly lines is becoming increasingly important. Simple and monotonous assembly tasks are increasingly being taken over by robots. At the same time, products are becoming increasingly complex. The future of assembly lines forms a homogeneous mix of humans and machines in production. uTrack serves both "sparring partners" best.
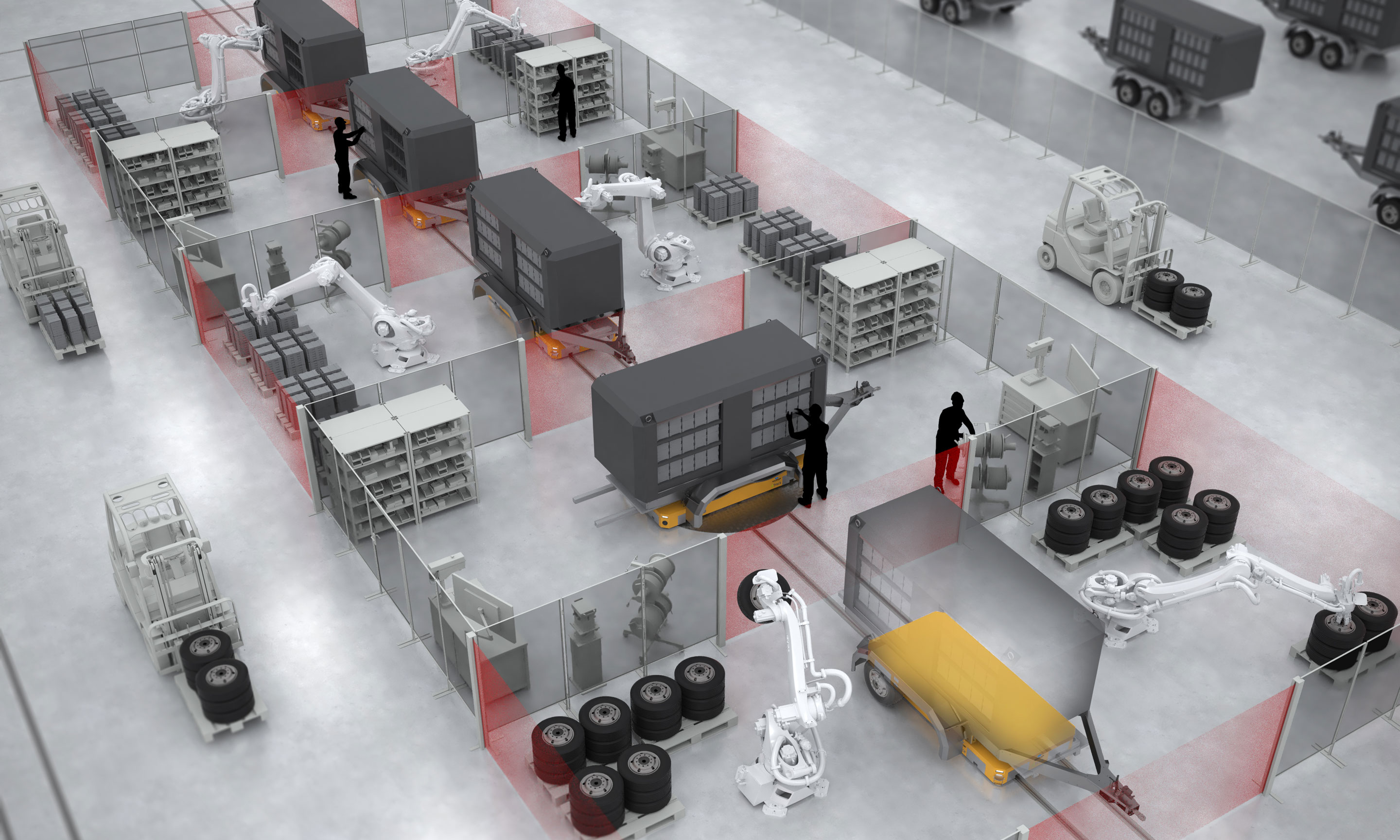
Precise placement of parts to the product.
Complete integration into the overall material flow of production.
Low overall height for ergonomic working.
Interaction with turning stations.